日立製作所:品質管理に Visual Inspection AI を利用した画像認識を導入し PoC で不具合判別率 100% を達成
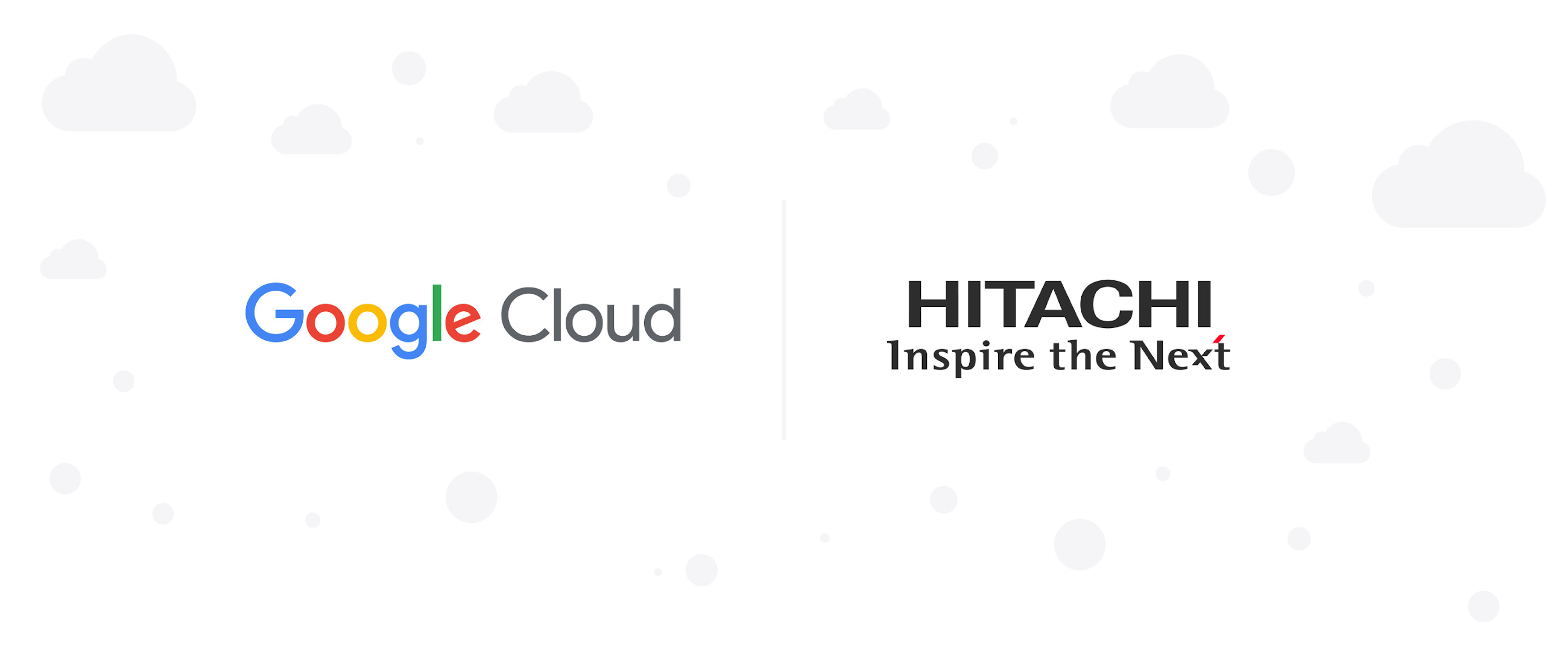
Google Cloud Japan Team
様々な分野で先進的な製品やサービスを展開している総合電機メーカーの株式会社 日立製作所(以下、日立製作所)。同社において社会インフラ・産業分野向け情報制御システムの製造・運用保守を担っている制御プラットフォーム統括本部 大みか事業所では、IoT やデータ分析ノウハウを駆使して社会課題を解決する取り組みの一環として、Google Cloud の Visual Inspection AI を利用した品質検査の精度や速度を向上させる PoC(概念実証)を実施しました。この PoC を担当した制御プラットフォーム統括本部 大みか事業所のメンバー 4 人に話を伺いました。
利用しているサービス:
Visual Inspection AI、Cloud Storage、Container Registry
AI による外観検査システムで製品の製造工程における不具合検出の検証を実施
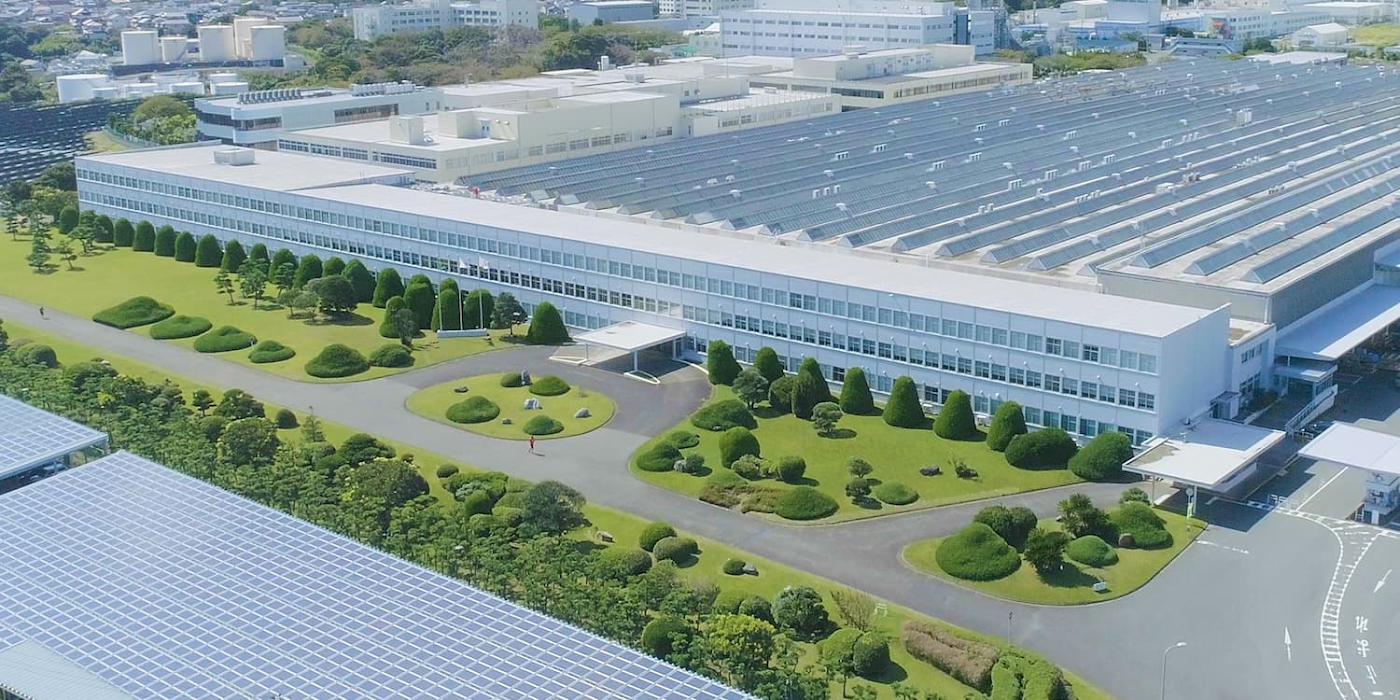
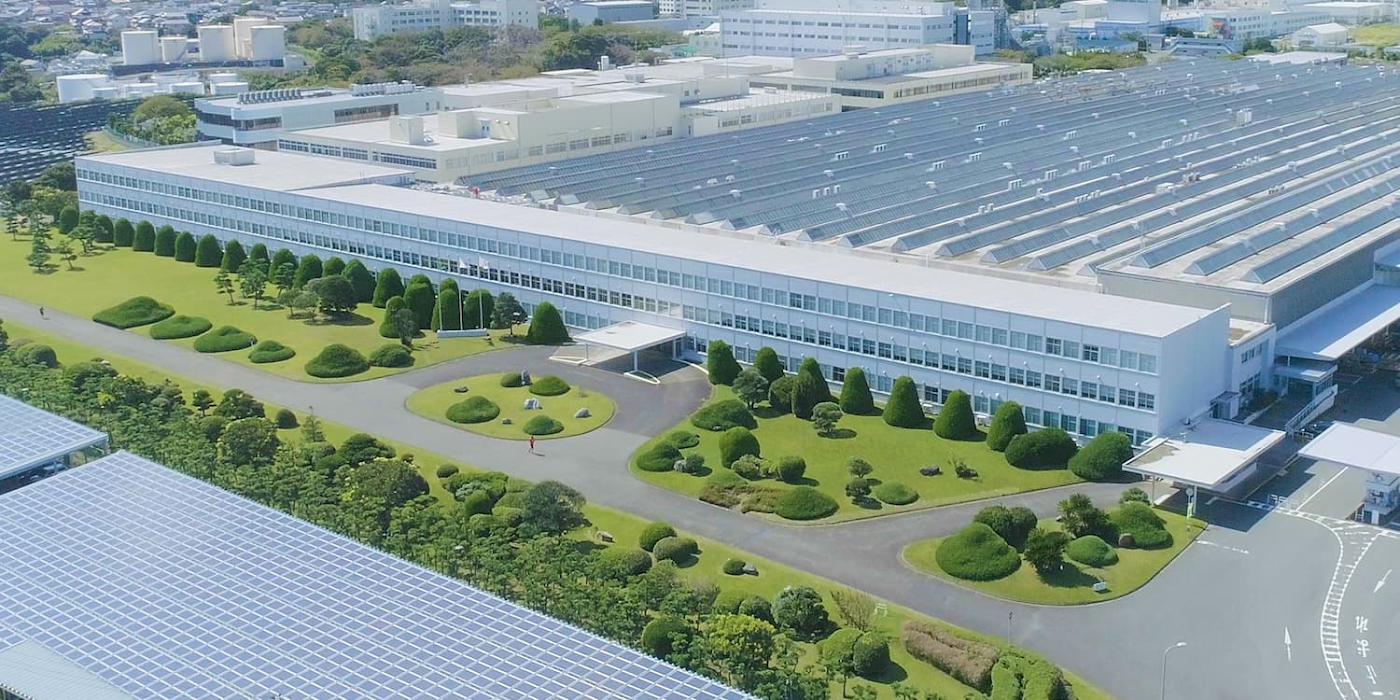
日立製作所の大みか事業所では、発電・送配電システムや鉄道運行管理システム、上下水道監視システム、製鉄所の生産システムなどといった社会インフラや産業分野向けの情報制御システムの製造・運用保守を行っています。日立製作所のシステムづくりの中核を担う大みか事業所では、IoT やデータ分析ノウハウを駆使して新たなビジネスの創出を目指す一方で、様々な社会課題の解決に向けた先進的な取り組みも実施しています。そのひとつが「大みかグリーンネットワーク」です。これは、大みか事業所がハブとなって地域やサプライチェーンを繋げるネットワークを構築し、社会全体のカーボン ニュートラルの達成を目指す活動です。大みか事業所自体がそのための実証実験のフィールドとなって環境負荷軽減や生産改革に向けた様々な検証を行っており、その結果を地域やサプライヤーに共有していきます。
大みかグリーンネットワーク活動の 1 つとして、大みか事業所の生産性向上を追求することで、継続的な節電を行い、CO2 削減をめざす環境モデル工場としての取り組みを推進しています。モデル工場としての新たな運用高度化に向けて、製品の製造工程における不具合検出を AI で自動化する外観検査システムを構築し、自社の工場でその効果を検証する PoC を実施しました。
検証の対象となったのは、制御盤の組み立てに使用する電線の接続端子の圧着作業です。端子圧着の良否判定は、現在は人による目視で行っていますが、検査に時間がかかることや、ヒューマン エラーが防ぎ切れないことなどが問題になっていたと、生産統括本部 モノづくり統括設計部 技師の高垣 昌之氏は語ります。
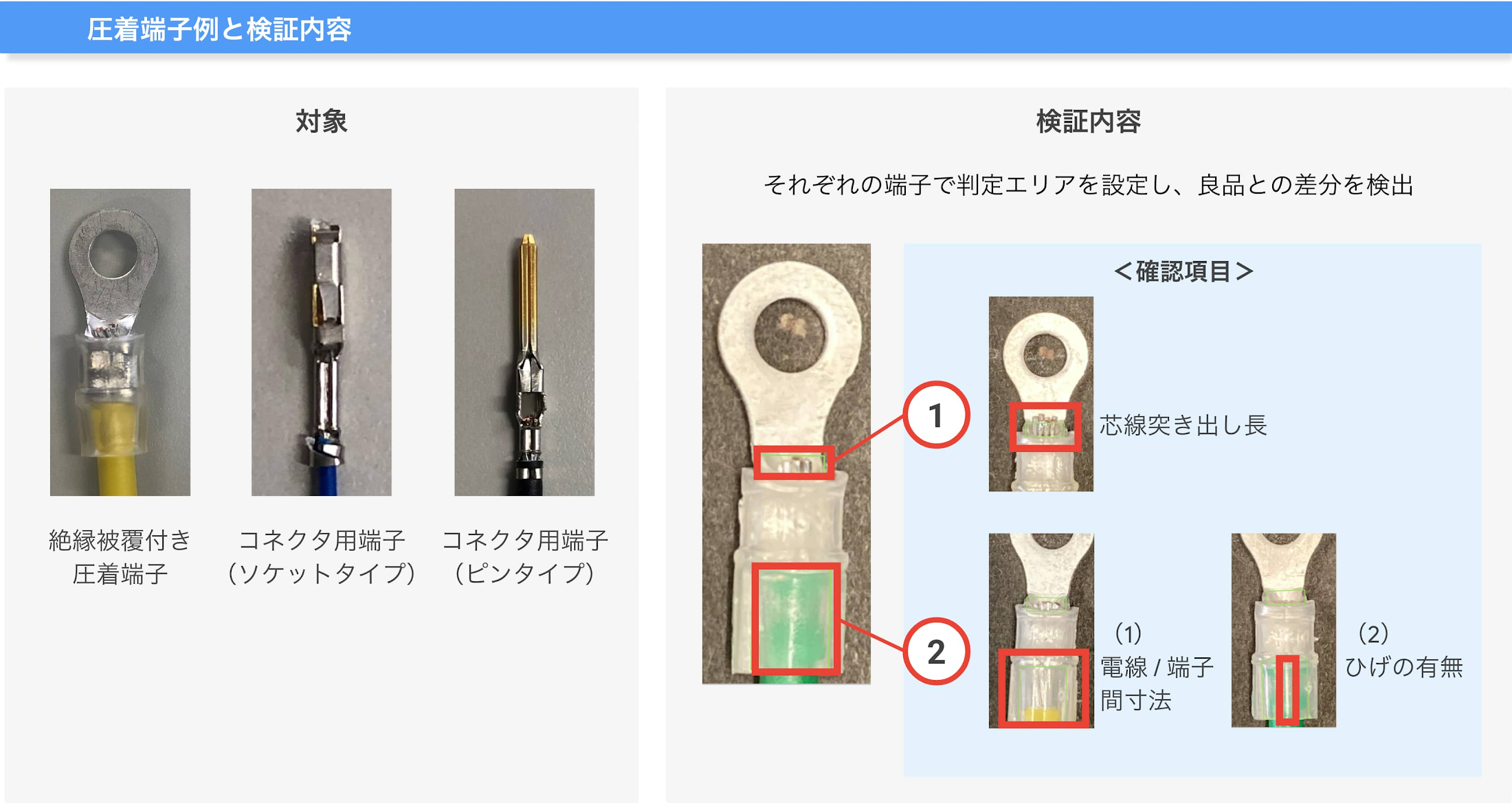
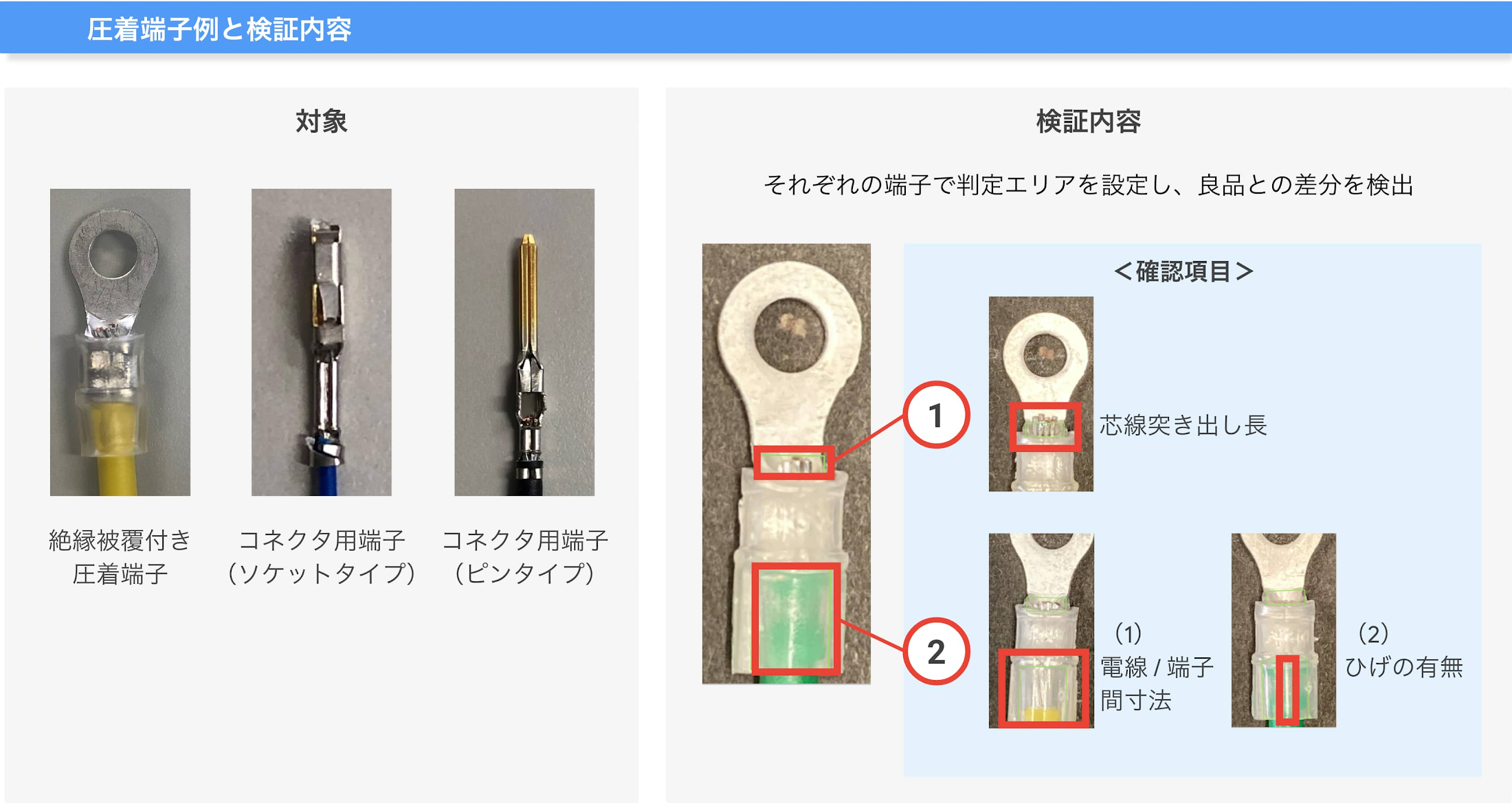
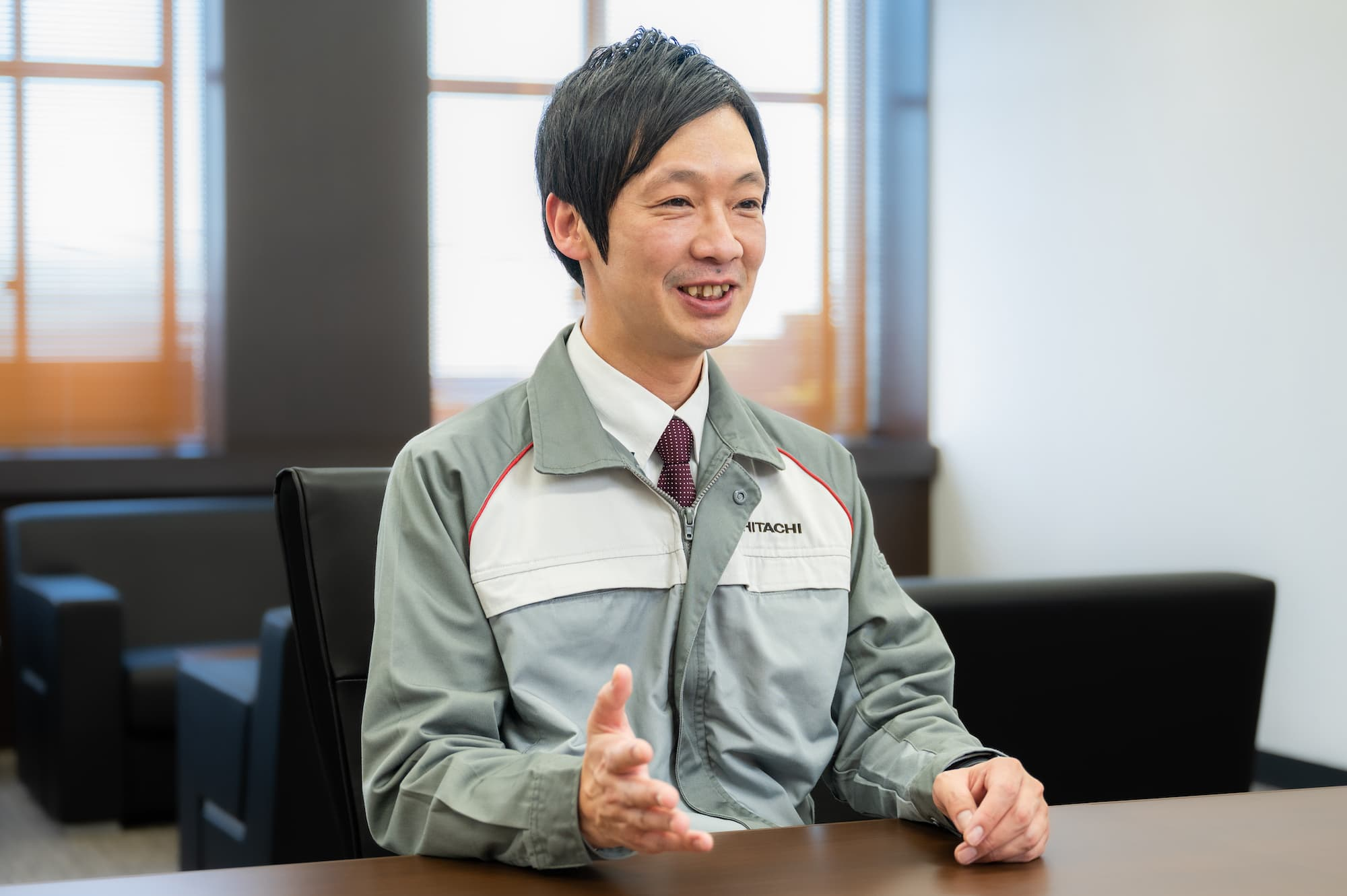
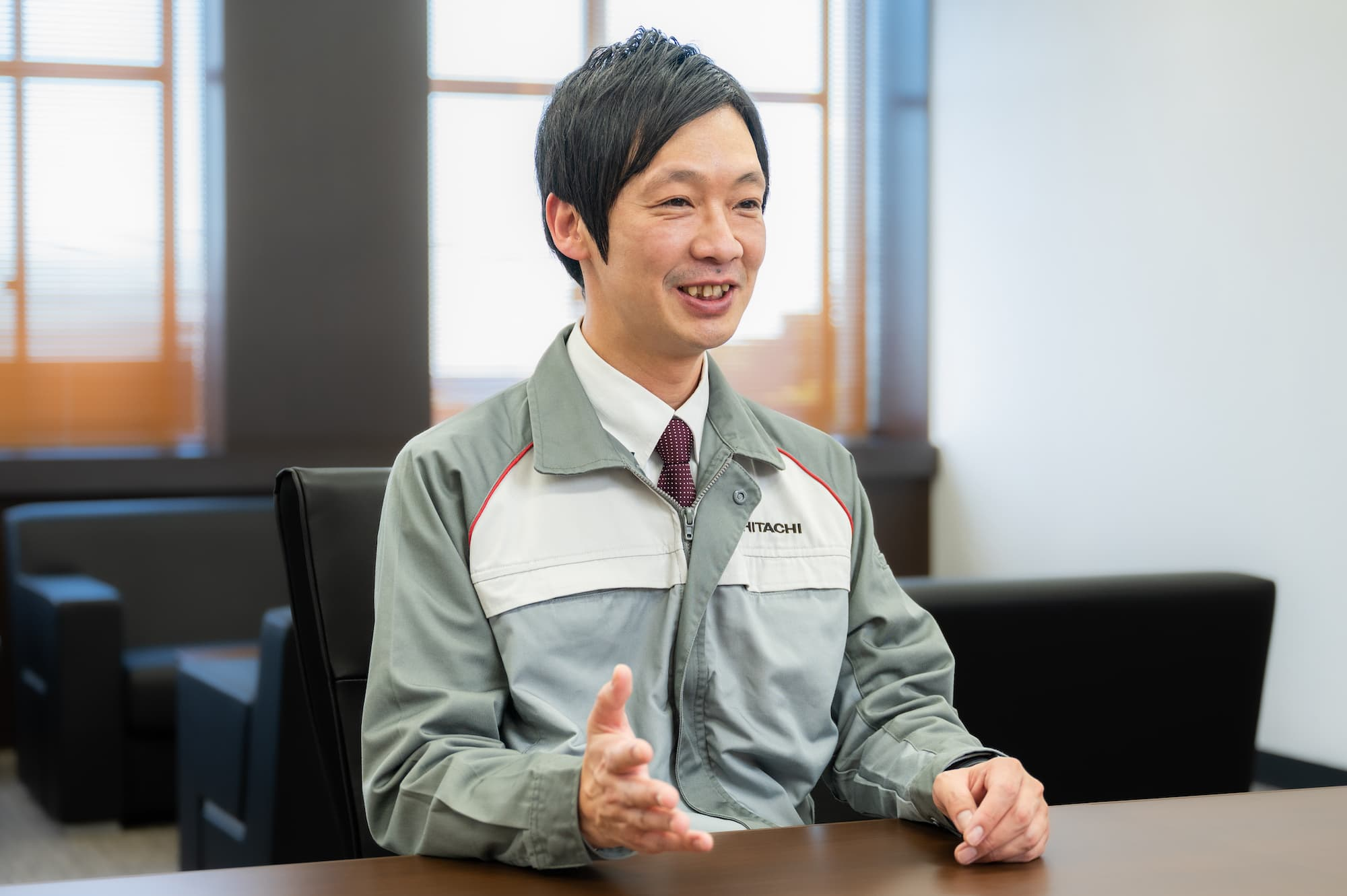
「当社の製造している制御盤は、1 度納入したらそのまま 10 年以上使われるような性質のものなので、接触不良などの不具合が起こらないように接続端子の品質管理には非常に気を遣っています。そのような中で、目視での検査というのは工数もかかりますし、どれだけ慎重にやってもミスを完全に防ぐことはできないという問題もあります。また、目視検査は社内資格を保有した作業員しか担当できず、今後の人材確保や世代交代なども考えると特定の人だけに依存するという体制は見直さなければならないという課題意識もありました。」
サービス・制御プラットフォームシステム本部 産業IoT&ロボティクス設計部 主任技師の齋藤 豪氏は、これらの課題に対する AI への期待について次のように話します。
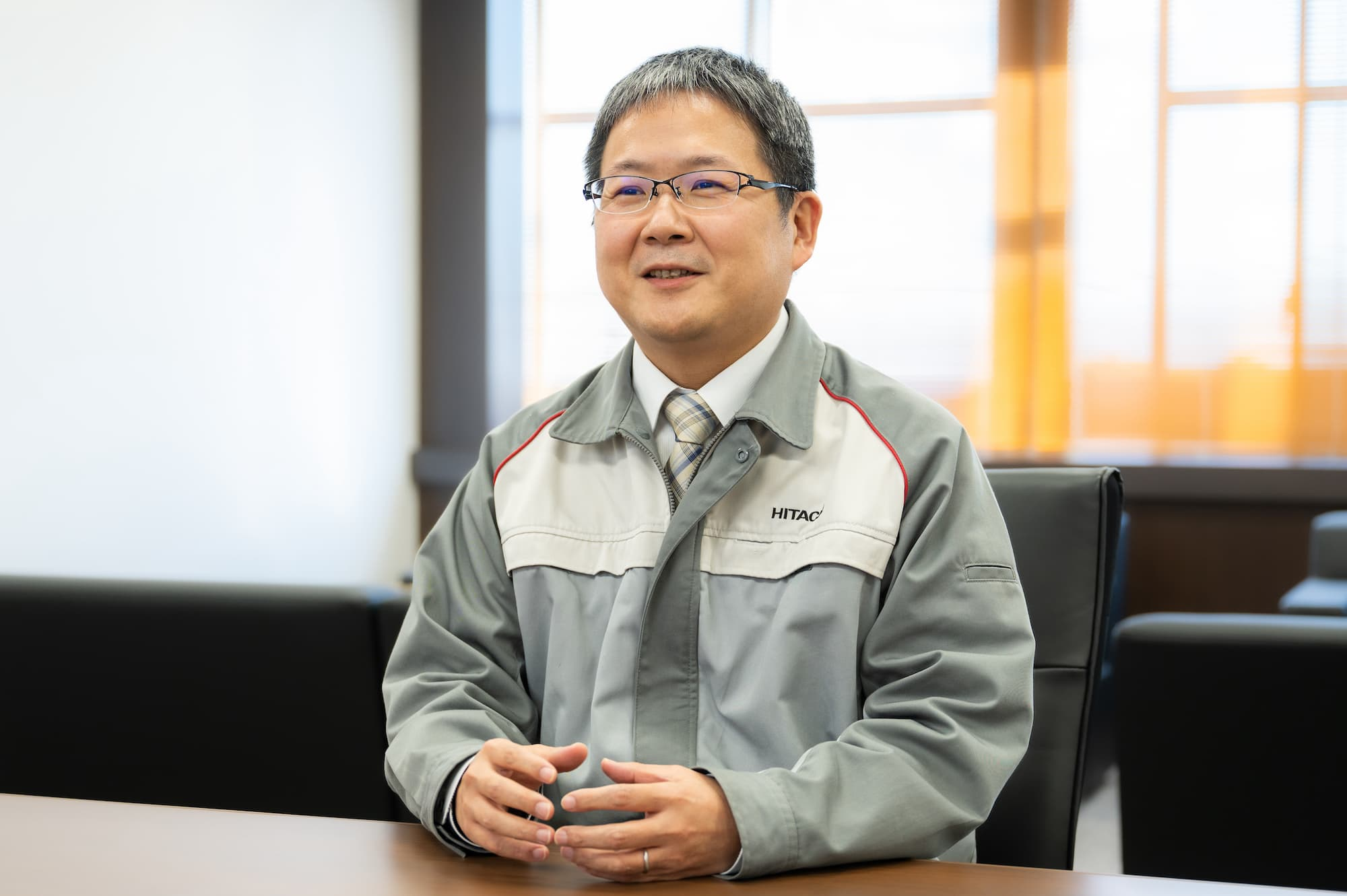
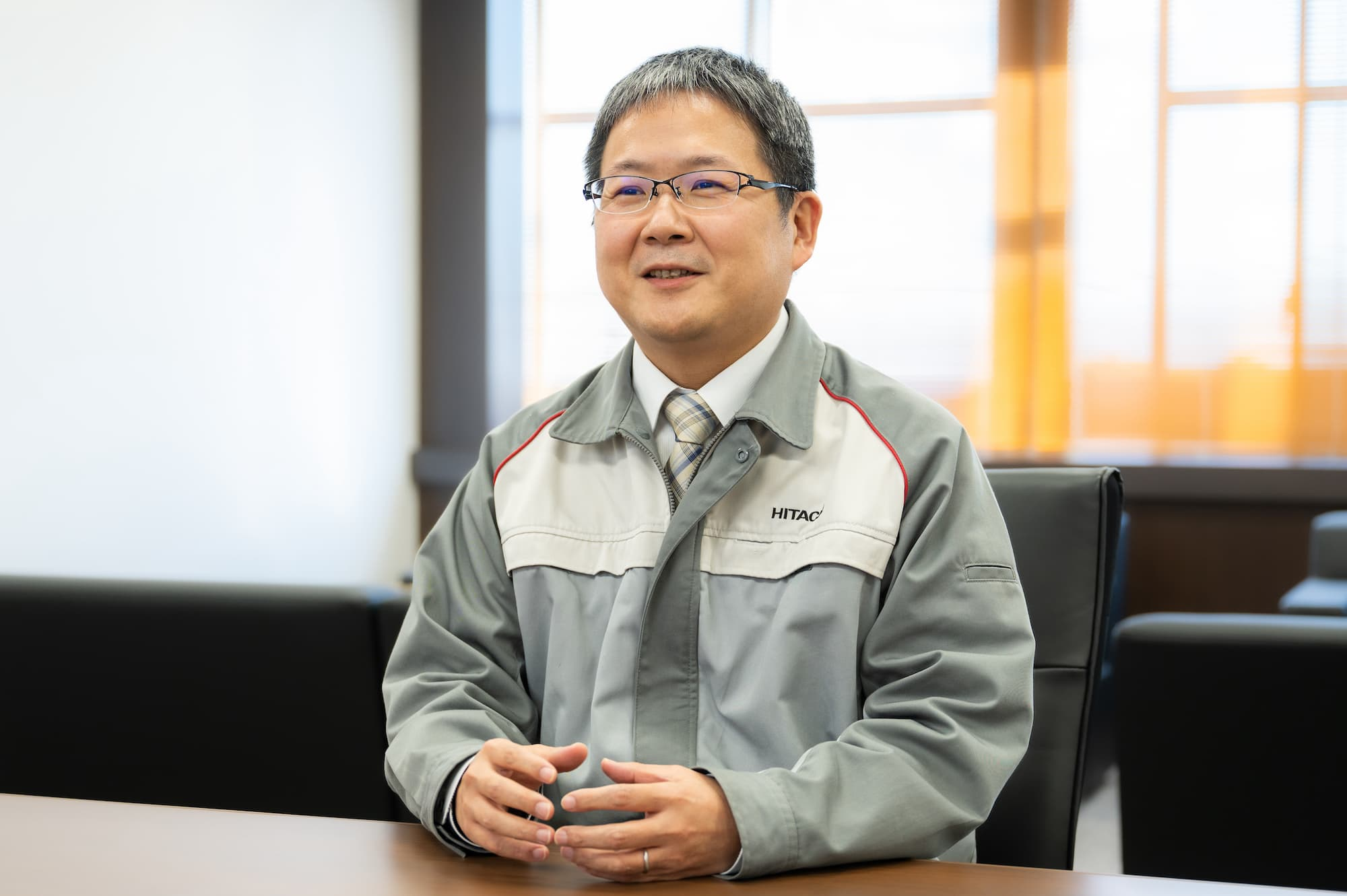
「一言に端子の圧着と言っても、ずっと同じものを同じように検査しているわけではなくて、例えば端子の形状や大きさ、ケーブルの太さなど、いろいろな要素でチェックする際の見え方が全然違ってきます。それらを正確に見極めるにはベテランの目が必要になるわけですが、AI であれば人の感覚に似た結果を出してくれるのではないかという期待がありました。」
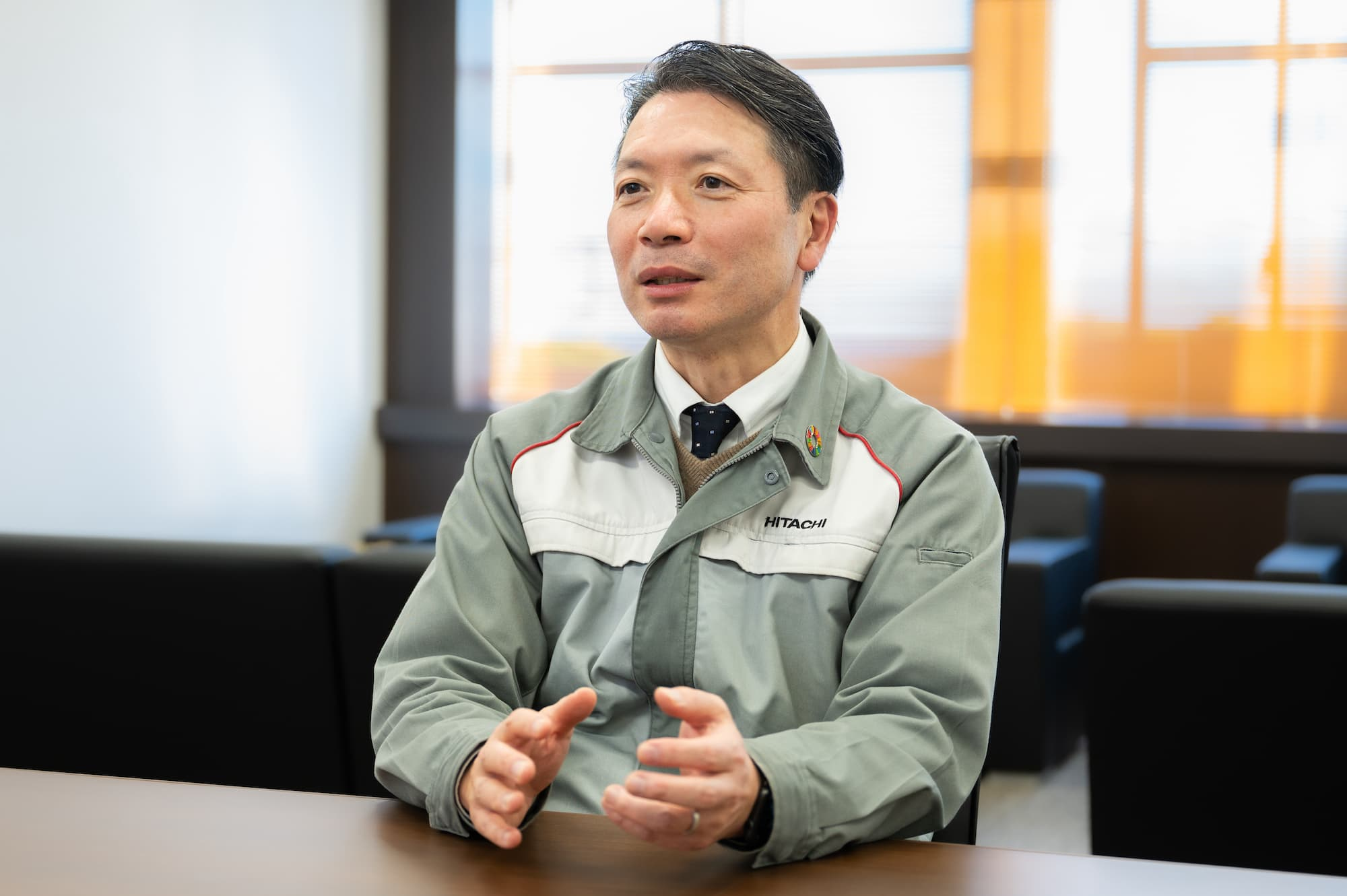
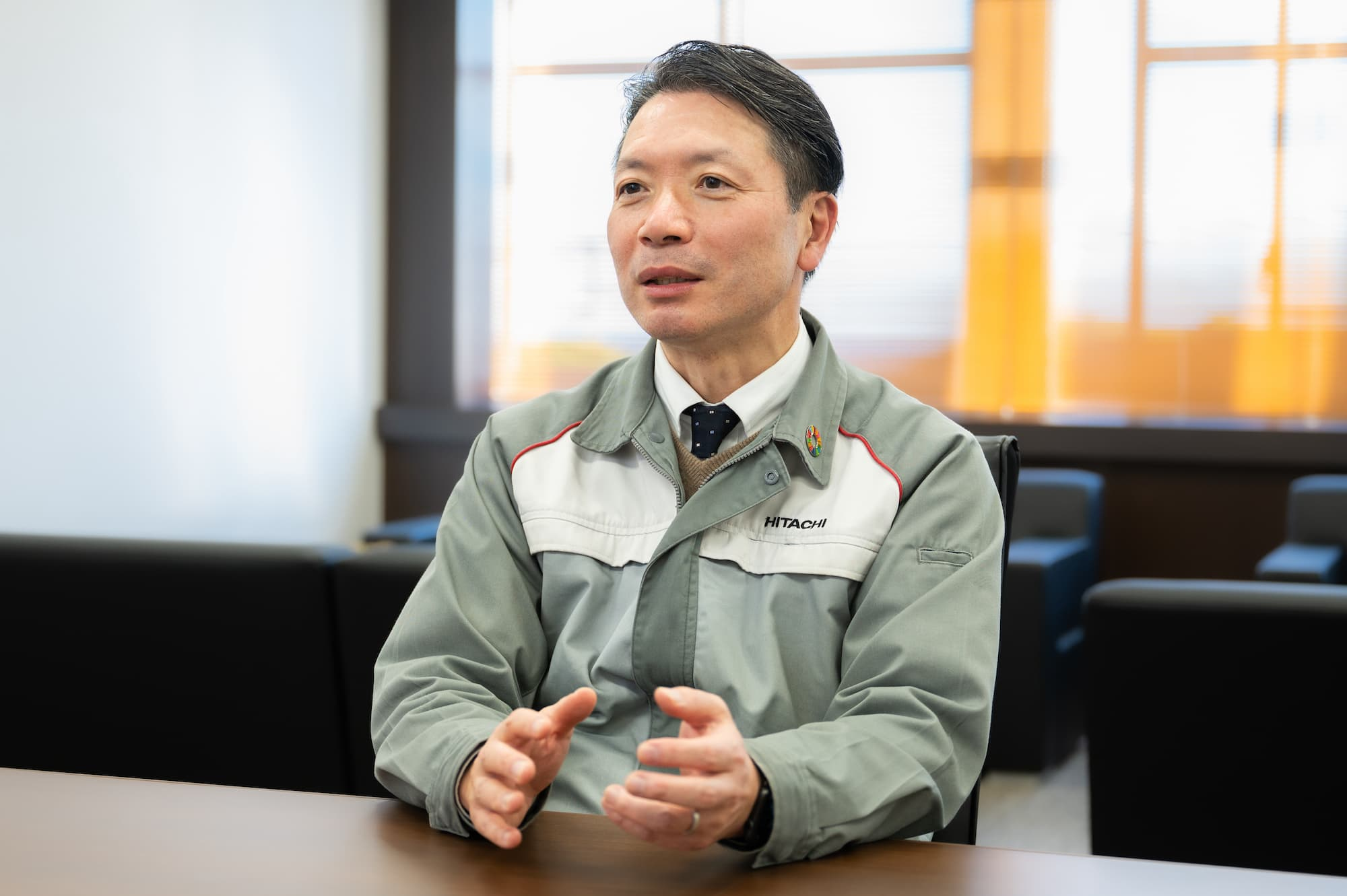
日立製作所では、AI を用いた制御が可能な日立制御エッジコンピュータ CE50-10 や、AI による外観検査アプリケーションによって、エッジ端末を使って AI で画像認識を行い品質管理に利用するソリューションを提供しています。しかし実際の現場にこれらのソリューションを導入する場合には、それぞれの顧客に合わせて個別に学習モデルを構築する必要があるため、さまざまな工場に広く展開するのは難しいという問題がありました。「この学習モデルを構築する部分を柔軟にして、もっと汎用的に導入できるようにしたいと考えたときに、クラウド サービスを活用するという選択肢が生まれました」とシニアストラテジスト 博士(工学)の入江 直彦氏は説明します。
今回の PoC は、日立製作所が展開する「Lumada アライアンスプログラム」の枠組みを活用して実施されました。このプログラムは、日立製作所がサードパーティのパートナーと連携して新たなイノベーションの創出を目指す取り組みであり、大みかグリーンネットワークにおいても企業や業界の枠を超えた協創を実現する基盤的な取り組みとなっています。Google Cloud もこのプログラムに賛同しており、日立製作所の持つ既存のソリューションと最適な形で連携することができるサービスを両社で検討した上で、Visual Inspection AI の採用が決まりました。
外観検査システムの構成を考える際には、「製造の現場で使える AI」を強く意識したと入江氏は語ります。
「一般的な AI サービスの場合、学習モデルを作成するにはさまざまなパターンを含んだ大量の画像を用意した上で、検査の内容ごとに時間をかけて検出の精度を高めるチューニングを行う必要があります。しかし実際には、工場の現場に AI のプロが常駐して学習モデルのチューニングを行うというのは現実的ではありません。そのため、現場のオペレータでも手軽に使いこなすことができる AI サービスが必要だと考えていました。Google Cloud の Visual Inspection AI であれば少ないサンプル画像から簡単に外観検査向けの学習モデルを構築できると聞いて、これを日立制御エッジコンピュータ CE50-10 と組み合わせれば理想的なシステムを構築できると判断しました。」
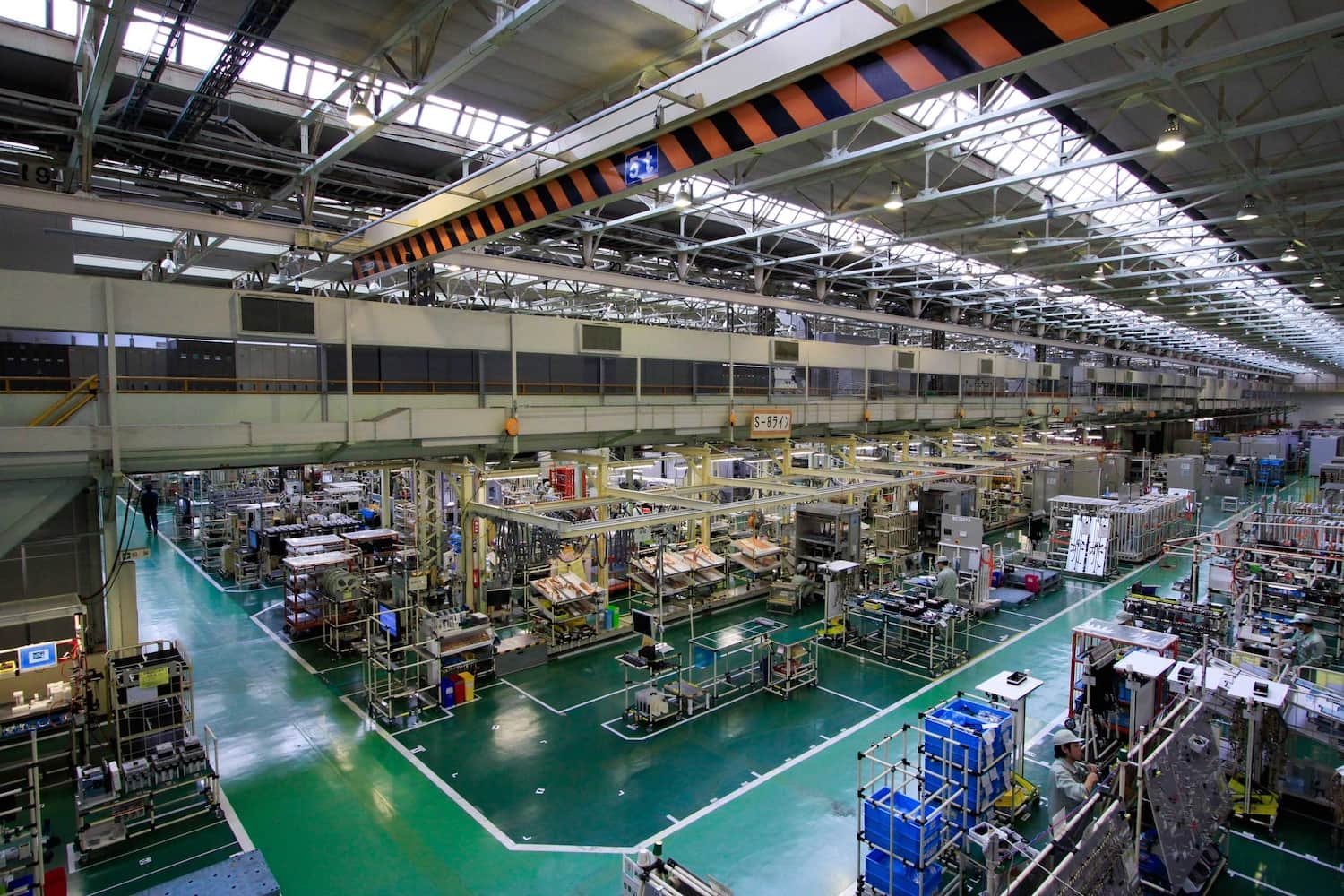
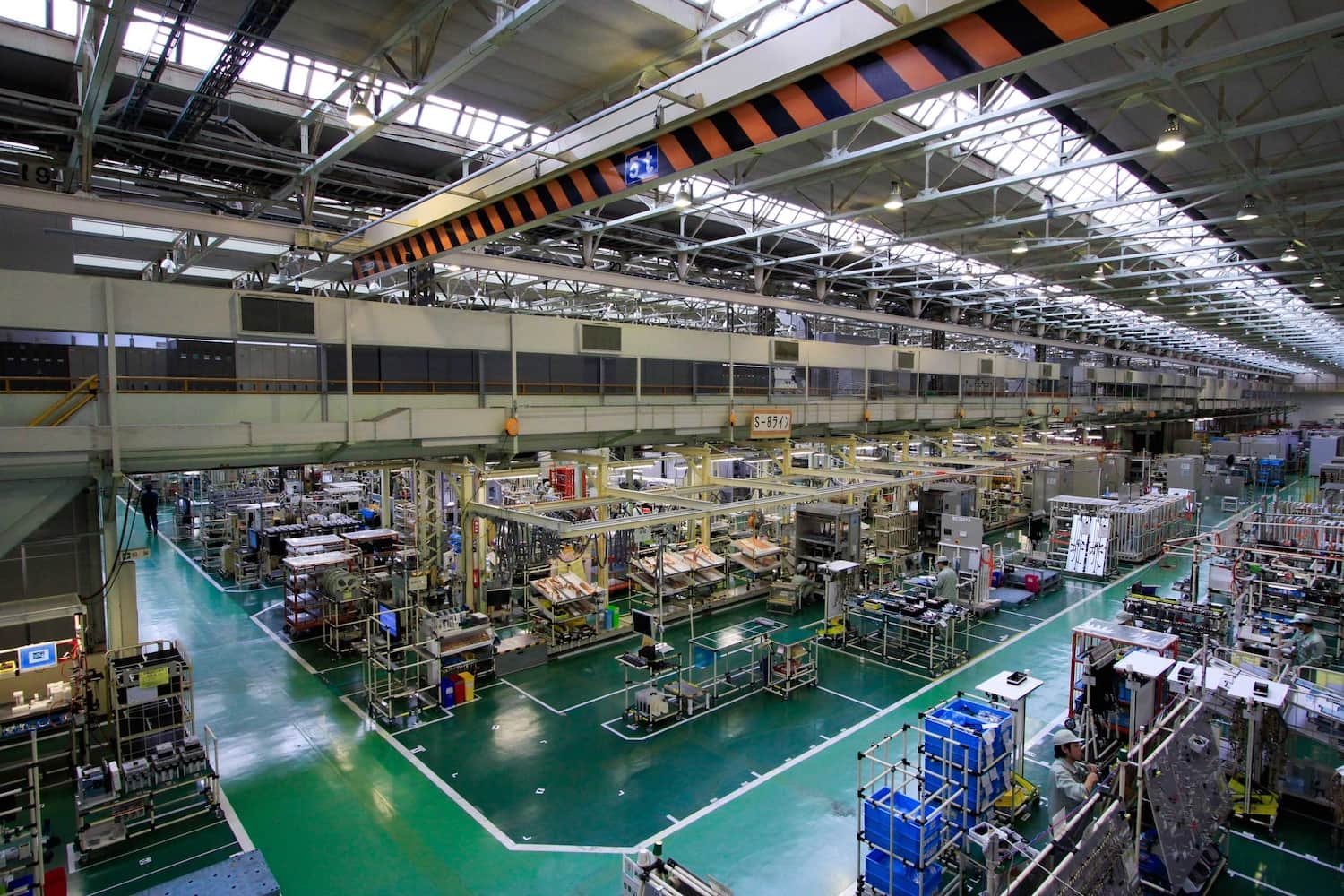
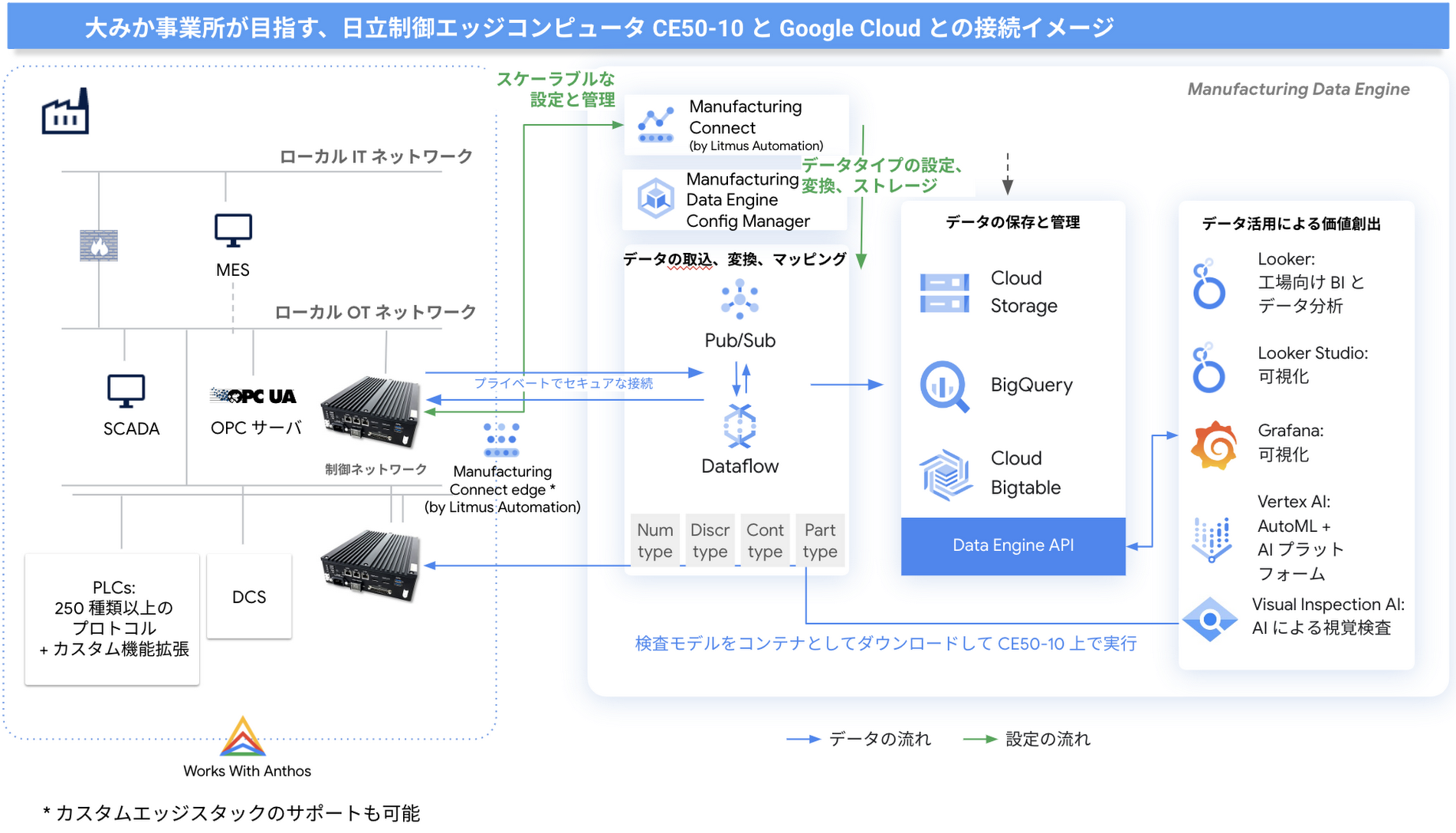
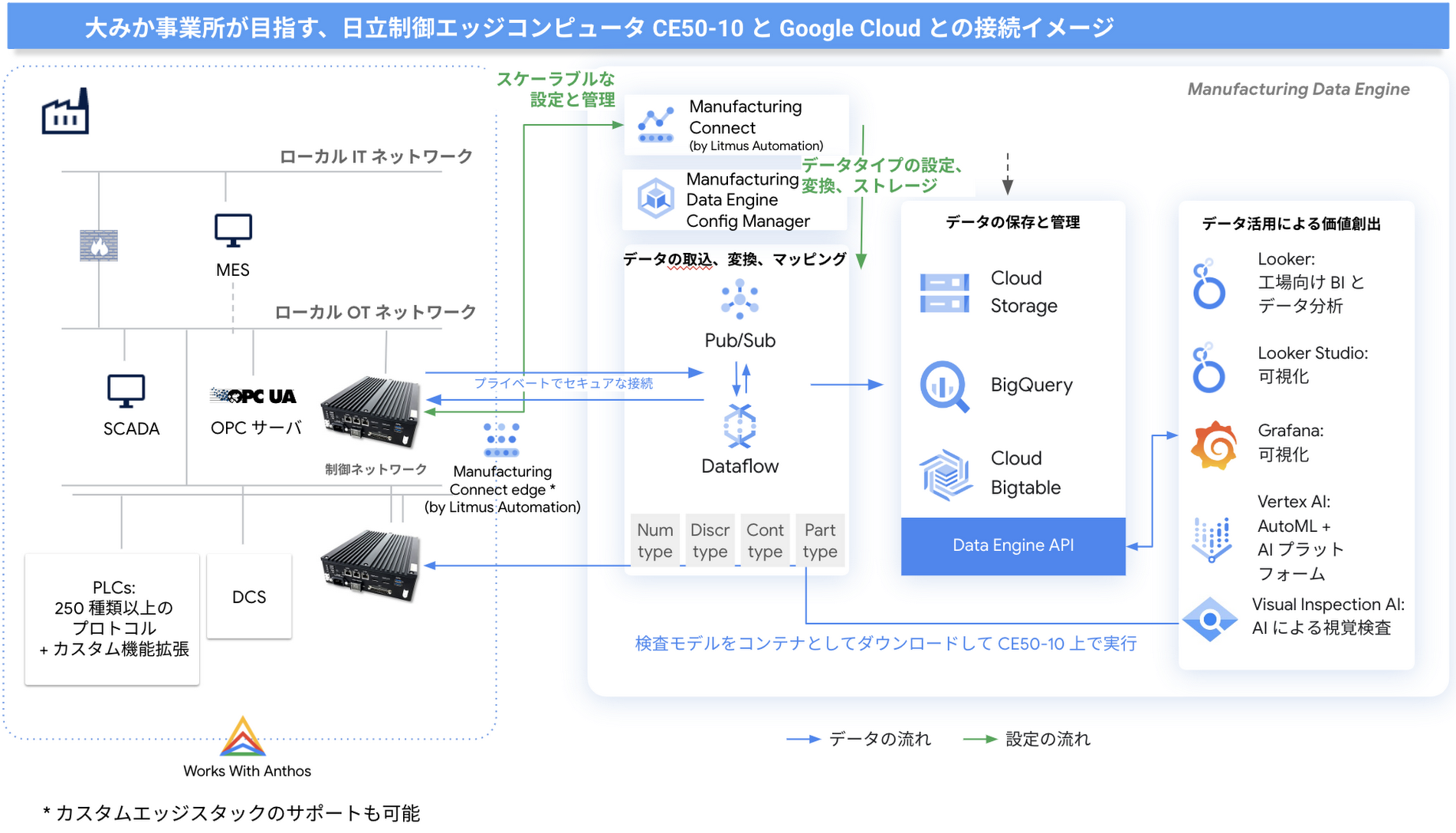
100 枚程度のサンプル画像で学習モデルの作成が可能、現場のオペレーションの中で「十分に使いこなせる」と実感
今回の外観検査システムでは、部品の傷などの検出に Visual Inspection AI の Cosmetic Inspection を、部品が正しく接着できているかどうかの検査に Visual Inspection AI の Assembly Inspection を利用しています。現場のエッジコンピュータと Google Cloud は VPN で接続し、学習の元になるサンプル画像のアップロードや、それを元に Visual Inspection AI が作成した学習モデルのダウンロードなどを行います。
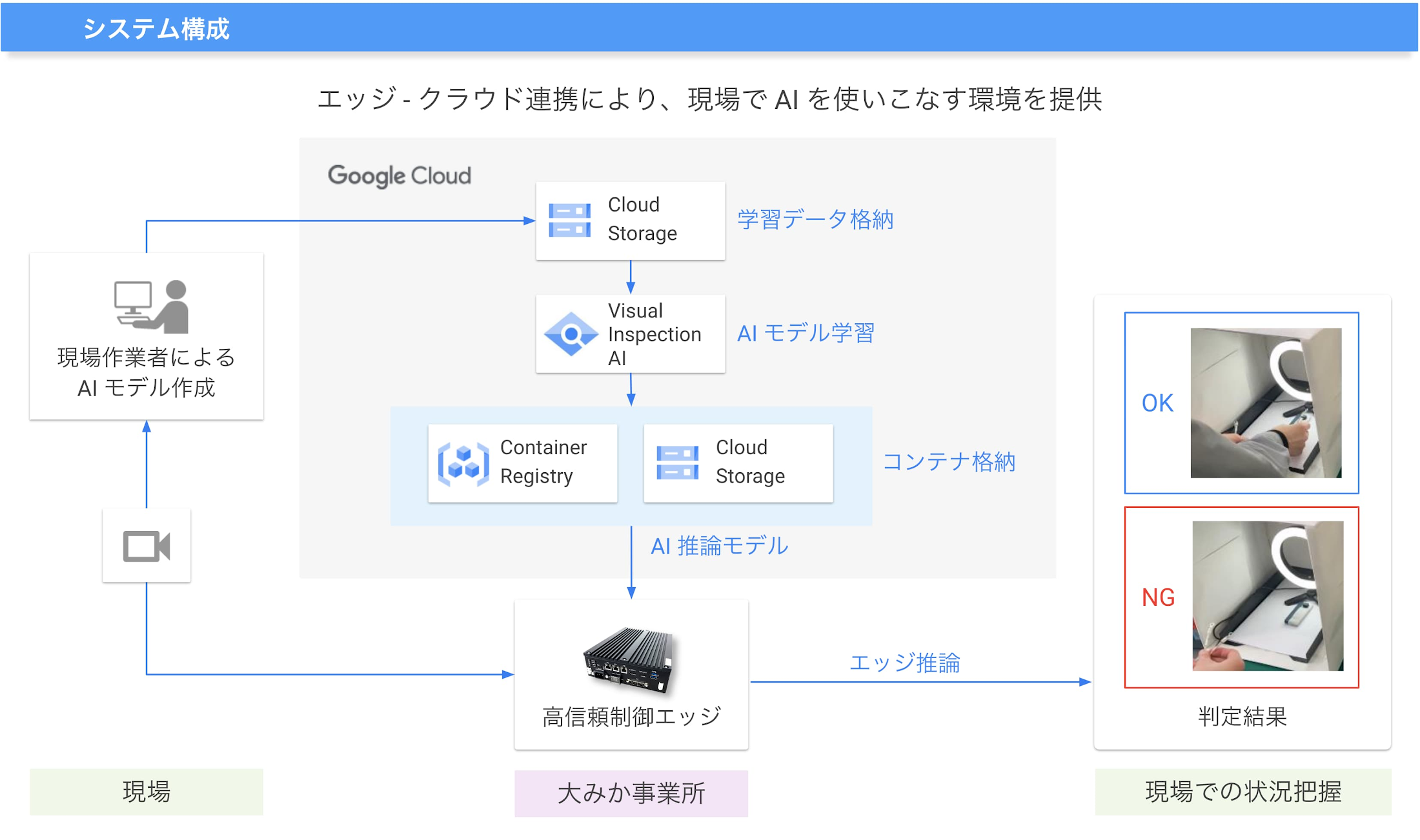
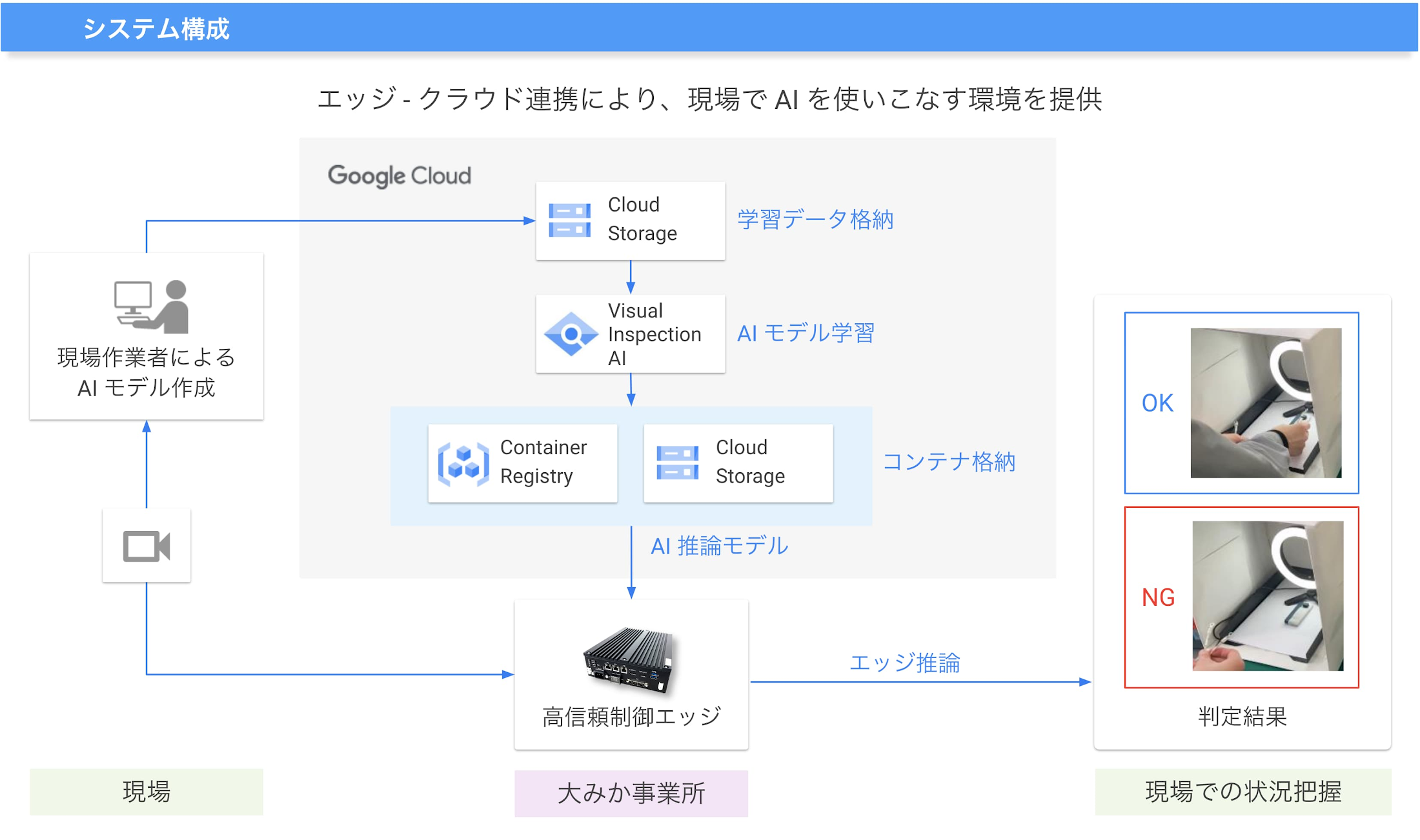
検証のためにサンプルとして使用した画像は約 100 枚で、画像収集にかかった時間を除けば、1 日程度の作業で学習モデルを作成することができたと高垣氏は言います。
「トータルで 5、600 枚ほどの画像を作って、そのうちの 100 枚程度を実際に使用しました。AI と聞いてどこか難しいというイメージがあったのですが、実際にやってみたら Visual Inspection AI のコンソール上のちょっとした操作だけで使えてしまい、率直に言って簡単だと感じました。これならば製造現場のスタッフも十分に使いこなせるという実感が得られました。」
実際の現場のオペレーションの中に組み込むためには何が必要かを確認することも PoC の重要な目的だったと齋藤氏は説明します。
「製造ラインは緻密な計算の下で構成されていて、どの工程にどれくらいの時間をかけるのかなどが厳密に決まっています。その中のどこに機械を入れて、どのタイミングで写真を撮って検査するのかなどを考えて運用設計を行う必要があります。技術検証に止まらず、どういう運用だったら製造ラインが成り立ち、どのような効果が見込めるかという仮説を立てた上で、それを実際に検証することができたのは非常に大きな成果でした。」
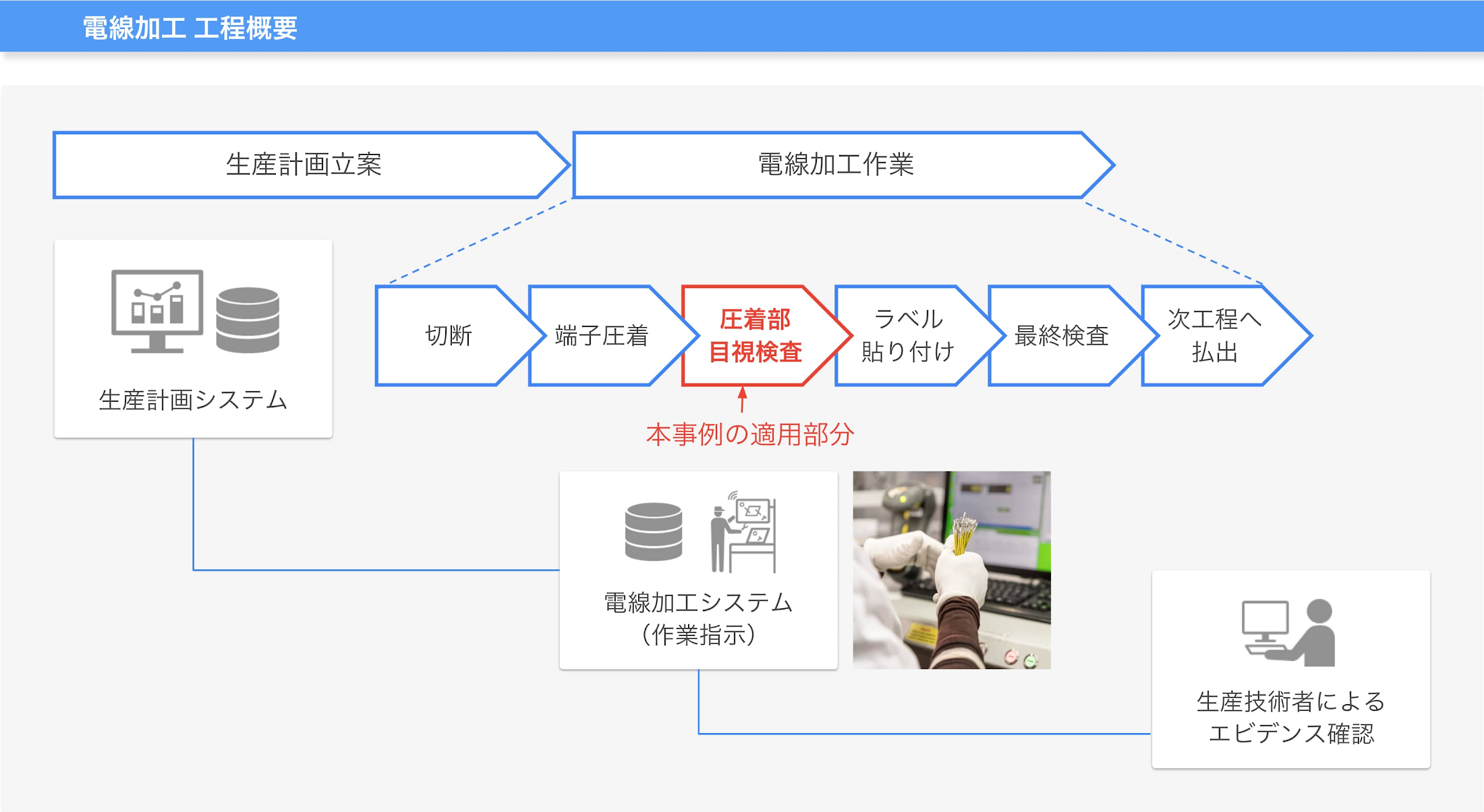
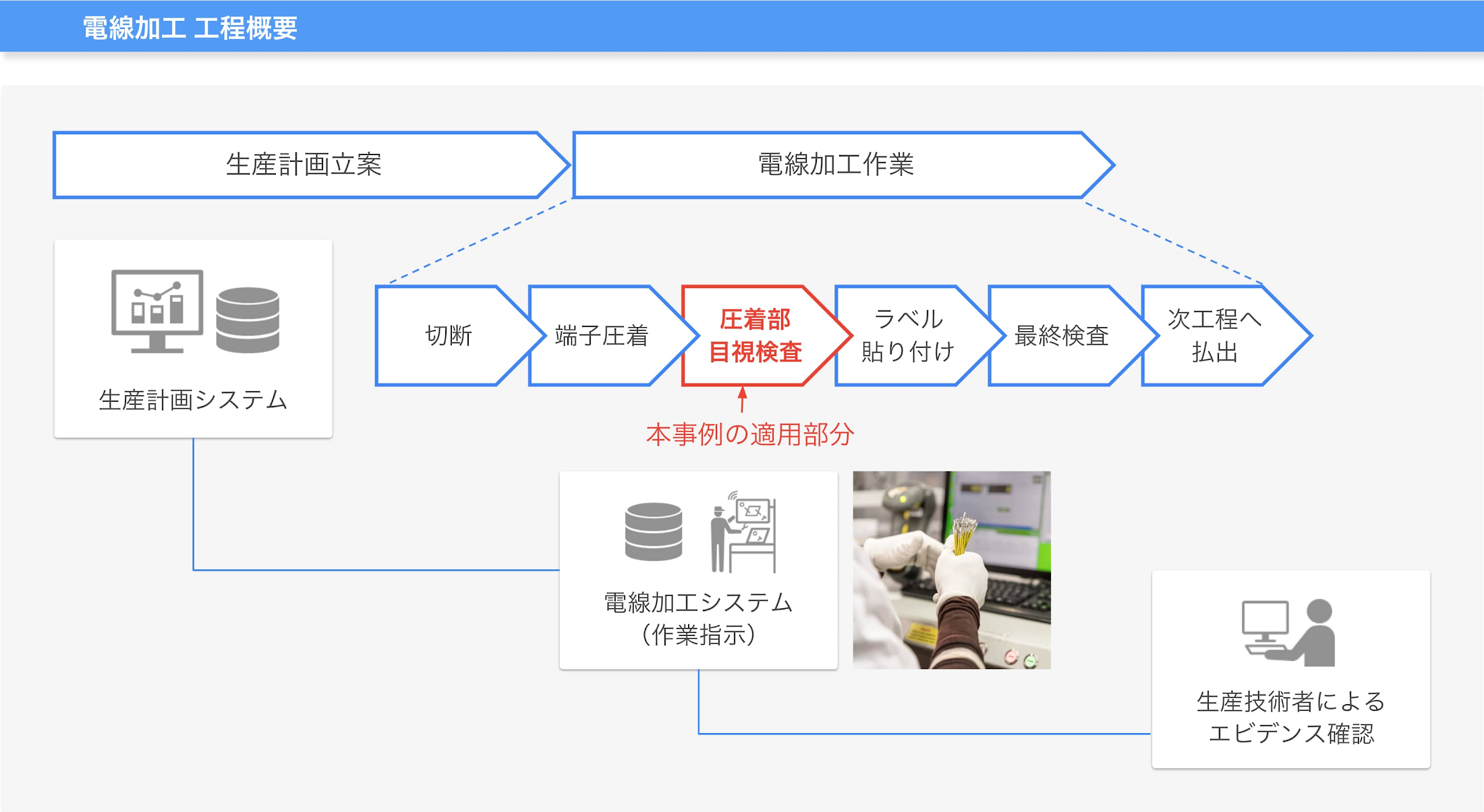
検査の精度についても、実用上問題ないレベルの結果を得ることができたとのことです。
「まず、不具合の判別率については 100% を達成しています。つまり検出漏れは無いということです。一方で虚報率は 13% と少し高めだったのですが、これは検証のために意図的に虚報を起こしやすいデータを含めていたことも影響しているので、実用上はもっと低い値に抑えることができるはずです。今回設計した運用モデルではさらに後の工程に目視検査があるので、ある程度の虚報は許容範囲だと考えており、現場の感覚としてはすでに実用レベルに達していると判断しています。」(齋藤氏)
ただし、実際に現場に導入するためには、判定速度をはじめとするいくつかの課題がまだ残されていると、サービス・制御プラットフォームシステム本部 新事業推進センタ 主任技師の加賀屋 俊一氏は補足します。
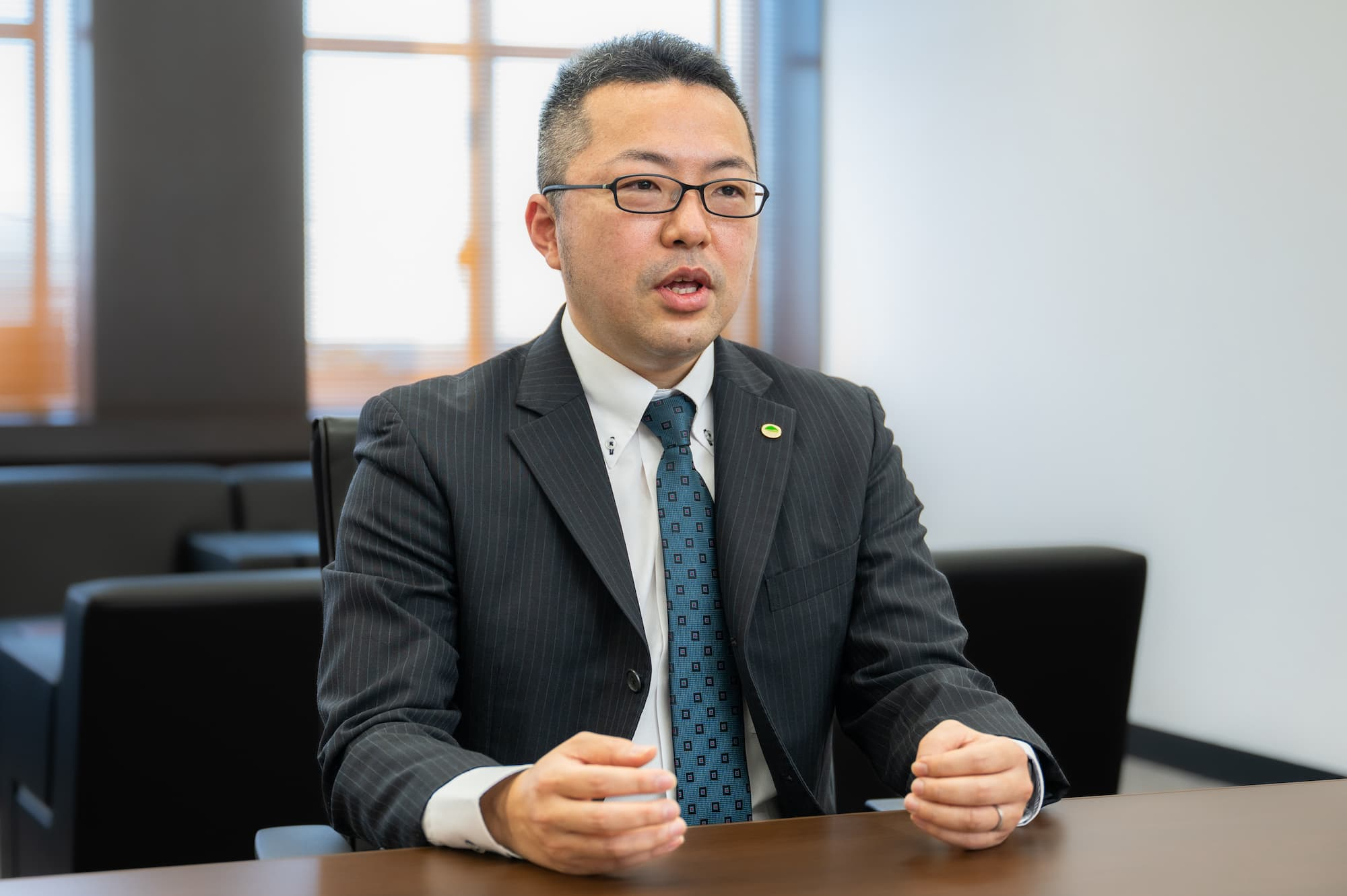
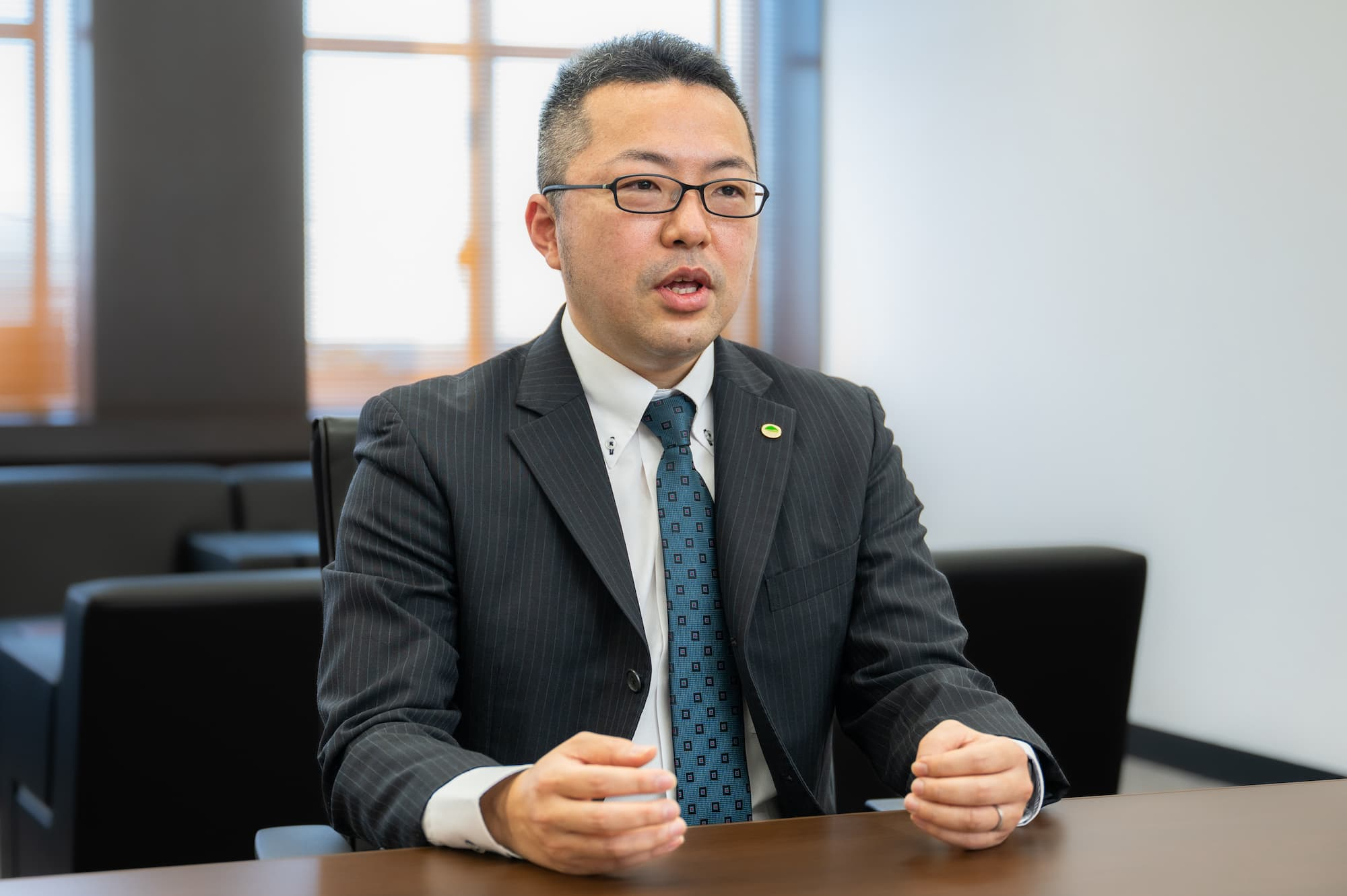
「今回の検証では、推論実行から結果表示までの 1 個あたりの判定に 4.5 秒かかっています。実用できるレベルではあるという当たりはつけられましたが、現場からは 2 秒まで縮めて欲しいという声が上がっており、結果表示部分などのチューニングが必要だと考えています。また、実際に現場に導入するためには、電線加工システムなどの既存システムとの連携や、機材追加に伴う製造ラインにおける動線の確認も必要です。それらの課題を解決するためには、次に何が必要かを考えてさらなる検証を重ねる必要があるわけですが、Visual Inspection AI であれば素早く学習モデルを作成して次の検証を行うことができます。この速度感はクラウド サービスならではの成果と言えますし、非常に重要だと思っています。」
排水処理設備の高度化に向けた実証実験でも Google Cloud の AI サービスを活用
大みか事業所では、大みかグリーンネットワークの取り組みの中で、最新の技術を用いて工場などの排水処理設備を高度化し、ダウンタイムの低減や規制遵守状態の見える化を行い、自然共生を図るための実証実験を実施しています。これは、センシング技術やエッジ AI を活用することで、配管の漏水予兆の検出や設備の故障予兆の検出、排水の処理状態の見える化、処理状態の自動判定などを行えるようにするという取り組みです。これらの設備によって排水の水質をより高度に管理できるようになれば、工場周辺の環境負荷を軽減することにつながります。
この実証実験においても、エッジ AI のための学習モデルの作成に Google Cloud の Visual Inspection AI を採用しています。具体的には、塗装に使用した排水を薬剤で浄化して川に戻すという過程で、正常に処理が行われたかどうかをエッジ AI による画像認識で自動で行えるようにします。
「排水処理設備の高度化は、環境に配慮した設計という観点での総合的な改善を目指したもので、そのための要素のひとつとして当社のエッジコンピュータと Google Cloud の AI が重要な役割を果たすことになります。このソリューションではセンサー情報の収集やデータ処理などといった部分でもクラウドの活用を予定しているので、AI 以外にも Google Cloud のサービスをもっと総合的に利用できるのではないかと考えています。」(加賀屋氏)
日立製作所の持つエッジ技術と Google Cloud の AI 技術を連携させた今回の取り組みについて、入江氏は次のように語ります。
「今回の PoC では、エッジが得意とする部分とクラウドが得意とする部分を融合させて、エンド ツー エンドで新しい価値を作ることができました。このようなケースを積み重ねて、将来的にはエッジとクラウドの境目をユーザーが意識しないで使えるようなよりシームレスなシステムを作っていきたいと考えています。その中で、ミッション クリティカル IoT を実現するための手段として、我々の技術と Google Cloud の先進的なクラウド技術をうまく組み合わせていけたらと思います。」
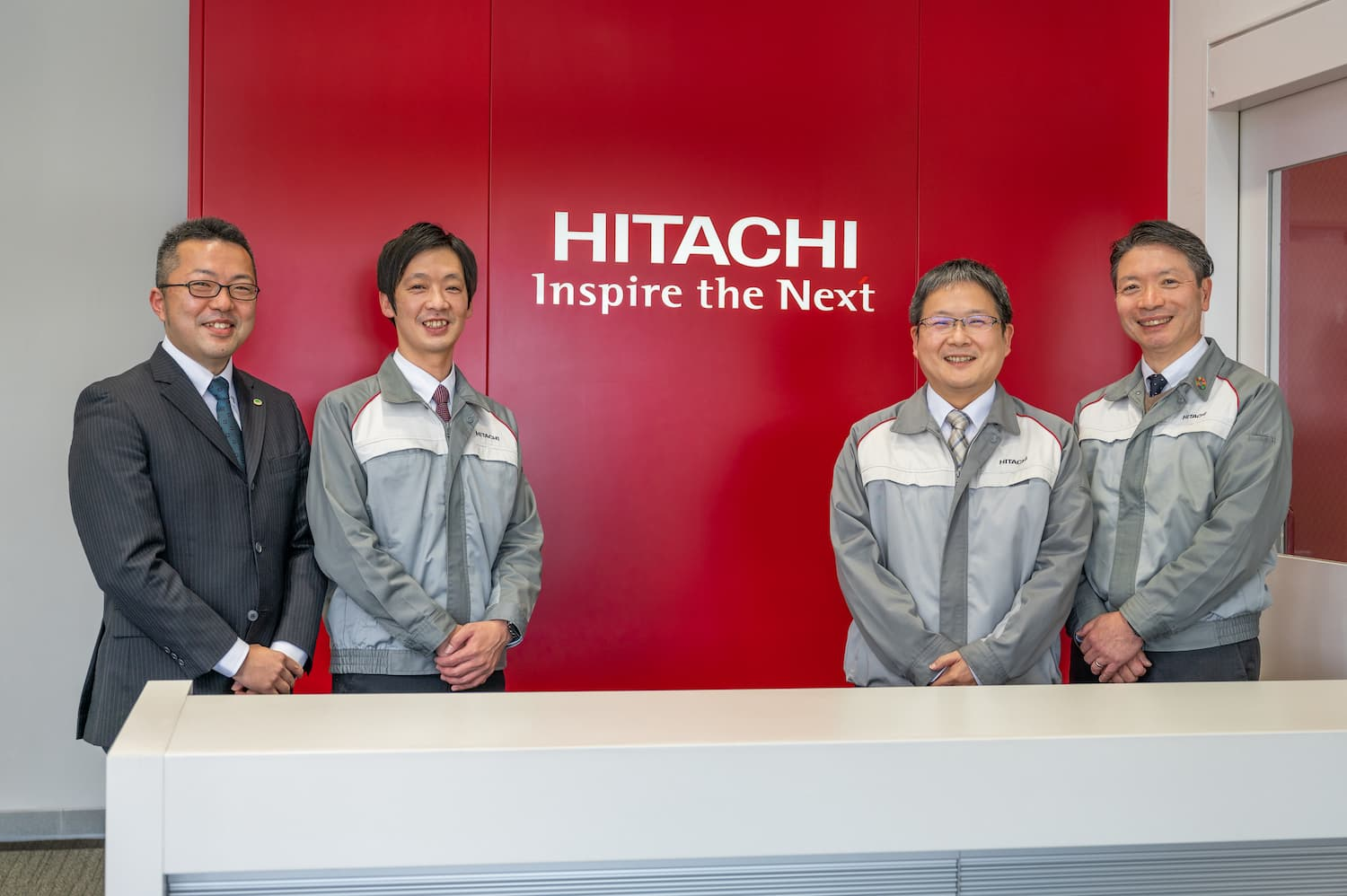
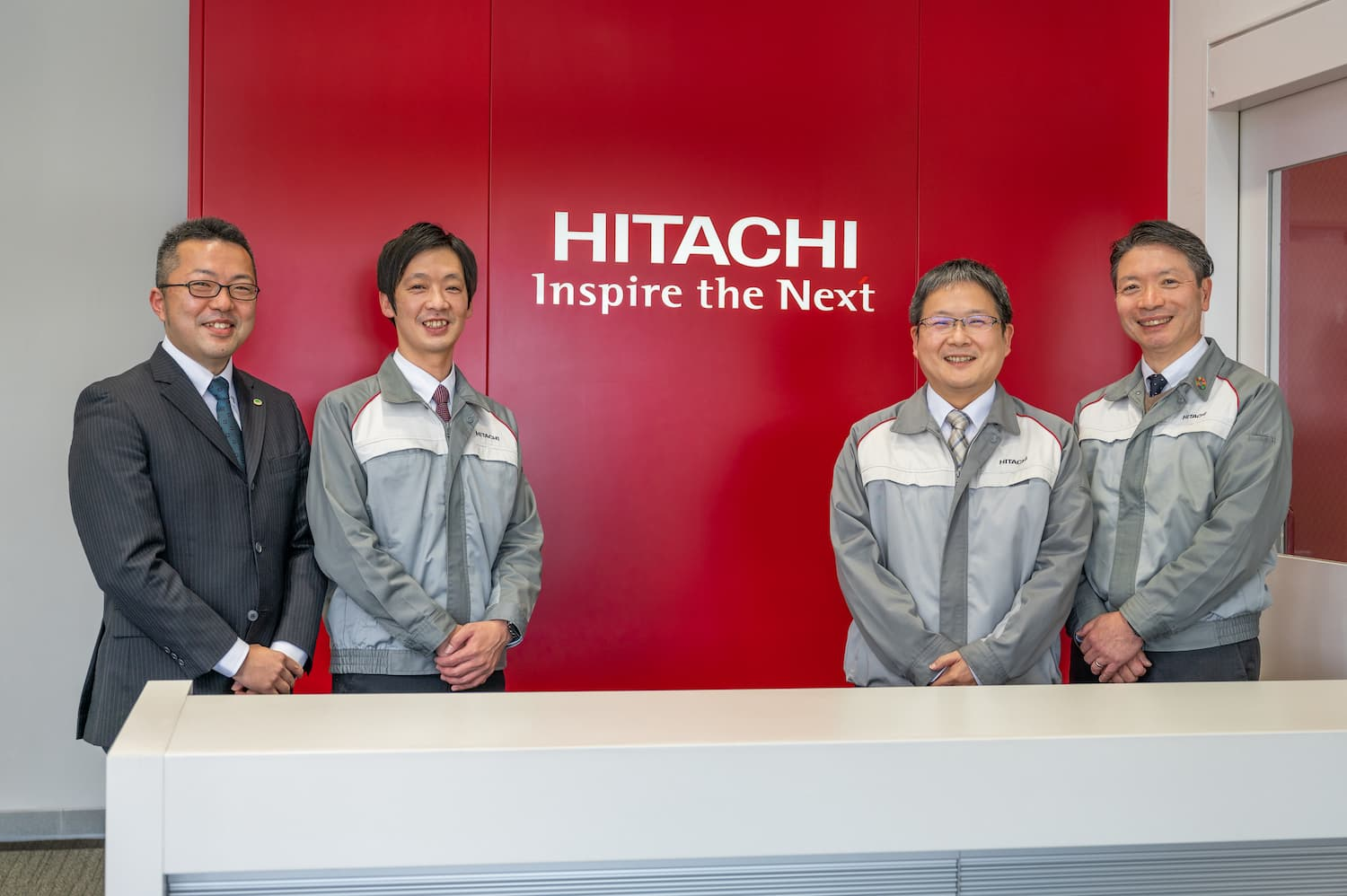
1920 年 2 月 1 日設立。IT、エネルギー、インダストリー、モビリティ、ライフなどの事業セグメントを中心として、様々な分野で先進的な製品やサービスを展開している総合電機メーカー。1969 年に操業を開始した大みか事業所では、発電・送配電システムや鉄道運行管理システム、上下水道設備の運転・維持管理システム、工場や製鉄所の生産システムなどといった社会インフラや産業分野向けの情報制御システムを提供。IoT やデータ分析ノウハウを駆使して様々な社会課題の解決や新たなビジネスの創出に取り組んでいる。
インタビュイー(写真左から)
制御プラットフォーム統括本部 大みか事業所
・サービス・制御プラットフォームシステム本部 新事業推進センタ 主任技師 加賀屋 俊一 氏
・生産統括本部 モノづくり統括設計部 技師 高垣 昌之 氏
・サービス・制御プラットフォームシステム本部 産業IoT&ロボティクス設計部 主任技師 齋藤 豪 氏
・シニアストラテジスト 博士(工学) 入江 直彦 氏
この記事の導入事例 PDF はこちらをご覧ください。
その他の導入事例はこちらをご覧ください。