The art of manufacturing possibilities: How AI and cloud build a virtuous cycle of optimization
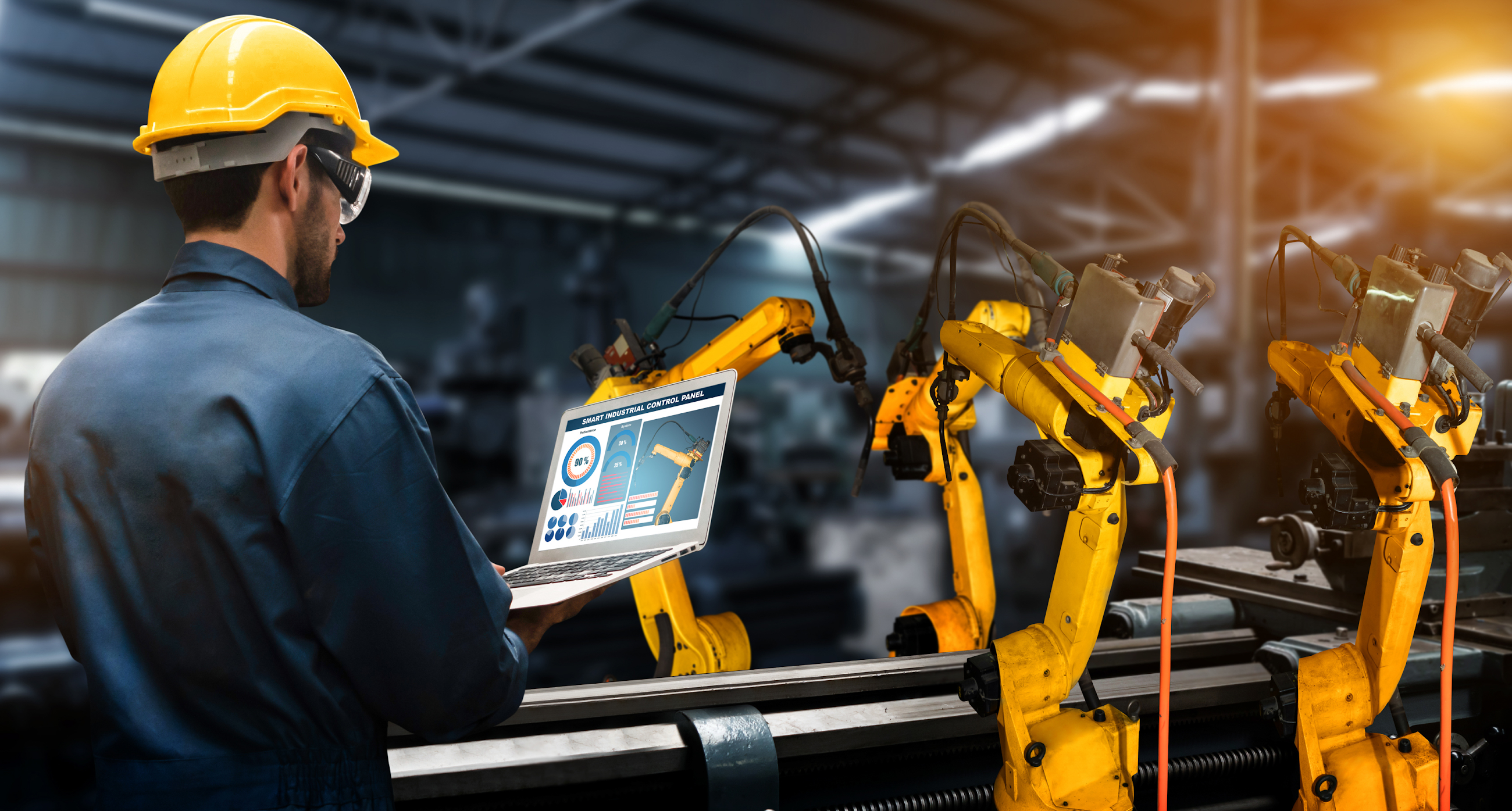
Matt Chaban
Senior Editor, Google Cloud
Manufacturing-specific cloud platforms and AI are unlocking new possibilities
A technician sits at a control panel, monitoring 20 production lines. A notification pops up: a valve needs to be replaced on one line before it fails. The technician authorizes an autonomous robot to move supplies from storage to the feeder system. Sensors in the storage facility note the drop in raw material and place an order with a vendor. AI cameras inspect quality and present data to the technician. The system takes in all variables of factory operations, measures output and efficiency in real time, and presents the technician with an easy-to-read dashboard.
The technician is at the center of this high-tech factory, but they are not alone. The system is constantly monitoring and adjusting, taking care of many of the tasks that would have been done by humans in the past. This frees the technician to focus on more strategic tasks, such as planning and problem-solving. As a result, the factory is more efficient and productive than ever before.
The future of manufacturing is here, and it is powered by AI.
The modern factory is a data-driven operation. From real-time process optimization to autonomous operations to the use of machine learning for quality assurance, and more, the art of the possible in manufacturing starts with a strong data foundation and burgeoning artificial intelligence tools. Factories are becoming more efficient, productive, and profitable. And they are able to bring new products to market faster than ever before.
“The use of data analytics and AI in manufacturing is still evolving, but leaders increasingly see it as a competitive game changer,” said Charlie Sheridan, global technical director for manufacturing, automotive, and energy at Google Cloud, noting that 85% of manufacturing CxOs see innovation as core to their organization’s future. “We are at that tipping point for data analytics and AI where the more we make machines more efficient through data, the more data we get to make machines more efficient. That virtuous cycle will open the door to more powerful AI and ML solutions which have the potential to not just advance but really revolutionize manufacturing.”
Manufacturing-specific cloud platforms have emerged in recent years to unleash the full potential of this data deluge and kick off this virtuous cycle. According to Google Cloud research, about 86% of manufacturing CxOs agree that their organization generates data and knowledge that directs their strategies, and creates a differential advantage against their competitors. With the right technology partners and cloud platform, they are increasingly able to take that data and knowledge to drive full data transparency, and to apply machine learning to optimize and predict business outcomes. These capabilities ultimately hold the potential to bridge digital and physical worlds, producing impact beyond what was previously imaginable.
Exploring the possibilities of data and AI on the factory floor
“All of this has to be grounded in real-world problems,” said Sheridan. “That’s the key. There has to be a problem statement that an organization is working towards. There has to be a value and a business case for doing this kind of investment.”
Companies like German printing press manufacturer Koenig & Bauer have used the virtuous cycle of data, efficiency, and optimization to great effect. Using Google Cloud’s Manufacturing Data Engine (MDE) to consolidate data silos to a single point of knowledge, the company has achieved faster, simplified evaluation of performance data from different sources, and identified previously hidden performance potentials. Using tools like BigQuery for data storage and Looker for business intelligence, Koenig & Bauer has been able to perform long-term trend analysis for better investment decisions.
F.S. Fehrer Automotive, one of the leading specialists for vehicle seating and interior components globally, hopes to consolidate its own data operations to make its production lines easier to manage. It has also started a pilot using Visual Inspection AI to monitor the quality of products as they come off the line. Within the next several years, the company plans to utilize data and AI to make the lives of its employees easier, streamline processes on the factory floor, predict maintenance and supply chain issues, and institute autonomous solutions up and down the operation.
Intralogistics innovator, STILL, has used data and machine learning to build ARIBIC ("Artificial Intelligence-Based Indoor Cartography"), a unique research project to create a live digital twin for warehouses to collect and analyze telemetry data to build the next generation of autonomous, smart warehouses. Data is collected from sensors integrated in forklifts or stationary sensors, then combined into a digital representation of the environment. From there, it’s then transferred into the cloud and enriched with semantic information. The result is a real-time 3D map that serves as a complete, up-to-date representation of the warehouse or factory floor.
Ceramics producer Villeroy & Boch is both a manufacturer and seller of stylish ceramic home goods products, such as bathroom sinks and dinnerware. It manages its data through cloud solutions like BigQuery and employs AI solutions like Vertex AI and AutoML, with applications that stretch from factory to showroom. The technology helps reduce production and energy costs — important for both the bottom line and many earth-conscious shoppers — while delivering value for customers through individual client outreach and sales recommendations.
“Customer experience and cloud maturity go hand in hand,” said Simon Floyd, the director of manufacturing and transportation industries at Google Cloud, citing an IDC report that indicates mature cloud users more effectively apply predictive analytics and data-driven insights to create experiences. “Understanding the customer through data provides valuable insights to drive innovation, but also for continuous improvement of the products they use and the factories that make them. The product and factory can create significant competitive differentiation that manufacturers are seeking.”
Stop buying machines, start marrying them to data
Until this point, manufacturing has been a game of adding machines. More machines meant increased productivity and efficiency. But the modern era has brought new tools that can make machines even better, without the need for huge capital investments.
Historically, manufacturers have suffered a disconnect between machines and their data. On one side, they have conveyor lines, robotic arms and gantries, injection molds, and so forth, all of which are part of the operational technology (OT). On the other side is information technology (IT), typically data and software that give a broad sense of what those machines have done.
OT and IT have traditionally been siloed, with different teams responsible for different aspects of the manufacturing process. The OT team’s mindset is often to buy machines and add AI to them. This can be expensive and lead to quandaries down the road, like vendor lock-in and incompatible data formats between machines and databases. The IT team can offer more flexibility by providing solutions such as unified data platforms connected to the cloud, and edge computing to bring the power of the cloud to the machine.
“There is a fundamental gap between information technology and operational technology systems,” said Floyd. “Bringing the two together is a smart move because it provides the opportunity to apply data and AI tools to industrial data, which can unlock new levels of automation and valuable insights for the enterprise.”
The case for convergence is clear. By working together, OT and IT can create a more efficient and agile manufacturing operation. To remain competitive, manufacturers need to find ways to bridge the gap between OT and IT. This will require a new way of thinking, one that is focused on collaboration and integration.
The art of the possible: autonomous factories
By converging OT and IT toward digital and cloud maturity, manufacturers can lay the foundation for a more autonomous future — a future where AI and automation can control and operate manufacturing processes without human intervention.
“The art of the possible includes factories that are increasingly autonomous,” Sheridan said. “You need different levels of maturity to get there, but as AI and automation continue to develop, manufacturers that embrace these technologies will be well-positioned to compete. We’re entering the so-called Industry 5.0, where 5G, AI, AR/VR, edge computing, 3D-printing, and so forth combine to create a vision of factories that are self learning, self adjusting, self healing and run on their own. Everything is working and driven through an AI system.”
For manufacturers, knowing the art of the possible means understanding who their customers are and what operational areas they can evolve to derive better business outcomes. Innovation and AI leadership open new possibilities for manufacturers to evolve customer experience, improve product development, optimize manufacturing operations, and build resilient supply chains in a scalable and sustainable way.
The autonomous vision for manufacturing has to start with a stable foundation of data. Each factory operation needs to take steps toward digital and cloud maturity before even more complex and innovative solutions can be added into the mix. It will be a process years in the making. To explore how manufacturers are working with Google Cloud, visit our Google Cloud for manufacturing product page.
Footnote: IDC White Paper, sponsored by Google, Digital Customer Journey for Manufacturers #US50419123, April 2023