The AI shift: More than a dozen reasons manufacturers are already seeing ROI on gen AI

Praveen Rao
Director, Manufacturing Industry Strategy & Solutions, Google Cloud
Many manufacturers are already putting gen AI into production — and seeing real returns across their operations.
Manufacturing, by its nature, has always been about bringing efficiency to the world. It was the very purpose of the first factories and assembly lines, and industrial leaders have been refining this work ever since. And with the rise of AI, edge computing, and advanced robotics, it’s starting to feel like we’re reaching a moment where manufacturing and automotive companies could experience productivity gains on the order of the initial Industrial Revolution.
For many organizations, it’s already happening, as we discovered in Google Cloud’s recent survey of hundreds of business leaders1 in the manufacturing and automotive industries. We have collected the responses and trends into a new report, The ROI of Gen AI in Manufacturing & Automotive Industries.
You can read all the findings in the report, but we wanted to share some highlights with you here, as well as the perspective of two industry leaders: Kevin Nolan, president & CEO of GE Appliances; and Natalie Bowman, Managing Director, Product & Experience Design at Alaska Airlines.
They reveal the ways gen AI is further enhancing quality control, safety, and customer experience across their businesses.
1. 60% have already moved gen AI use cases into production
With nearly two out of three organizations in the manufacturing and automotive sectors deploying gen AI1, it indicates their strong belief that AI technologies will drive productivity, enhance security, and spur innovation. Companies that have yet to adopt gen AI may be falling behind their competitors, as the ability to leverage gen AI for tasks like design optimization, predictive maintenance, and quality control can provide a significant advantage in terms of product quality and customer experience.
However, while 60% have implemented gen AI, the scale and complexity of these implementations varies and the most effective use cases are still being determined.
"Some of the challenges of getting gen AI from pilot to production are ensuring you have quality data, effective prompt engineering, and technical efforts aligned with business objectives — so testing as well as collaboration across teams are key. It's also vital to manage expectations and provide a safe environment for experimentation. Not all projects necessarily need a pilot-to-production mentality. At GE Appliances, democratizing safe AI tools like Gemini for Google Cloud has empowered employees to innovate daily, driving successful AI adoption from the ground up." - Kevin Nolan, President & CEO of GE Appliances, a Haier company
2. 86% running gen AI in production and reporting increased revenue estimate gains of 6% or more
Many early adopters are already seeing gen AI pay off in a number of areas, leading to increased productivity and higher revenue2. The fact that almost seven out of eight respondents who have experienced revenue growth estimate meaningful gains suggests a potential competitive advantage for those who have embraced these technologies.
While there is a strong correlation between the organizations investing in gen AI and those that are seeing revenue growth, other market factors may be at play, such as a penchant for strategic thinking and risk taking at these manufacturers.
"Defining ROI can be challenging because we’re all learning this new tool together. However, the investment versus potential has made it an easy decision to start using gen AI. Experimentation and early adoption are key. The organizations willing to take these steps will be the ones leading transformation." - Kevin Nolan
3. 43% reporting productivity improvements indicate employee productivity has at least doubled
The significant productivity gains demonstrates the potential of gen AI to not just automate tasks but fundamentally change how work is done, leading to a dramatic increase in output. Early adopters of gen AI are already experiencing tangible benefits — including a doubling of productivity for almost half3 — setting the benchmark for others and establishing a significant competitive advantage. While these early gains suggest a serious opportunity for wider adoption of gen AI across manufacturing and automotive sectors, it's important to note that achieving such significant productivity gains may require a commensurate investment in technology, infrastructure, and training.
Nonetheless, with such large potential gains on the table (and the manufacturing floor), those who have yet to fully invest might look closely at where the greatest potential lies within their organization to achieve quick, sizable, impactful AI wins to begin advancing their work in this area.
“People are often hesitant to share how much they’re using AI to help them do their jobs. Removing the stigma around using it is one of the barriers to understanding its impact on productivity. We encourage employees to use gen AI to become more efficient at their jobs. We need to be more transparent that it’s not just okay to use it, but that it’s the expectation.” - Natalie Bowman, Managing Director, Product & Experience Design, Alaska Airlines
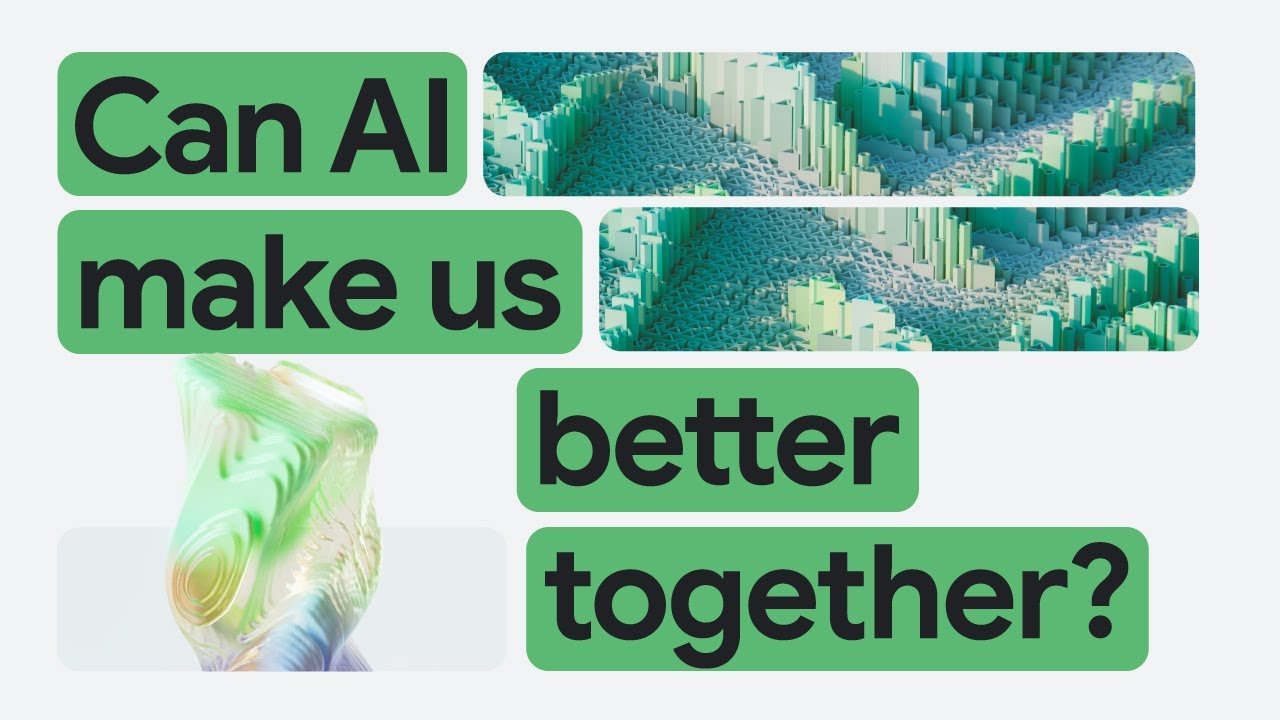
4. Only 1 in 4 organizations have comprehensive C-level sponsorship of gen AI adoption
Strong executive support for gen AI adoption can be crucial for its success, yet only a minority of organizations surveyed said they did1. There’s an opportunity for the remaining 74% of manufacturing and automotive organizations who don’t have comprehensive C-level sponsorship on gen AI adoption to build closer collaboration with CEOs and CFOs to reach these goals.
Leadership support has proven key for ensuring resources are allocated for successful implementation, departmental alignment, and collaboration. With executive buy-in, organizations are more likely to take calculated risks and explore promising gen-AI applications.
“Getting C-level buy-in starts with showing the business impact. We want to make our employees’ jobs easier. Our brand is about care, and giving our employees tools that improve their jobs shows them that we care about them and invest in their happiness. That resonates with our C-level executives.” - Natalie Bowman
1Total market - manufacturing & automotive (global): n=364
2Manufacturing & automotive organizations currently leveraging gen AI in production and reporting increased revenue: n=111
3Manufacturing & automotive organizations currently leveraging gen AI in production and reporting productivity improvements: n=154
4Total market - manufacturing & automotive organizations with at least one use case in production: n=351